Temperature Induced Dimensional Variation in Extrusion
Gregor Hiesgen1a, Kenny Saul1b, Chris Rauwendaal2
Rauwendaal Extrusion Eng., Inc. 10556 Combie Rd PMB 6677 Auburn, CA 95602 USA. 530.269.1082, chris@rauwendaal.com
Abstract. Melt temperature variations occur in all polymer extrusion operations using screw extruders. These thermal non-uniformities can result in dimensional variation in the cross section as well as in the extrusion direction. The melt temperature distribution is determined by the viscous dissipation and the conductive heat transfer in the polymer. Conductive heat transfer by necessity requires differences in stock temperatures. Polymers have very low thermal conductivity. As a result, melt temperature non-uniformities in extrusion are often substantial. Temperature differences in the range of 10-30°C are not unusual, especially in large extruders (100-mm diameter or larger).Cross sectional melt temperature variation results in problems like non-uniform wall thickness, ovality, and shape distortion. Axial melt temperature variation results in dimensional variation along the length of the extruded product. One example of such variation is waviness in pipe extrusion; this is a common problem in pipe extrusion operations. This paper will present an analysis of axial dimensional variation caused by temporal melt temperature variation. The analysis will employ an analytical approach to quantify the dimensional variation as well as computer simulation using the software chillWARE®. Keywords: melt temperature variation, waviness, ovality, dimension variation, cooling simulation, product quality,chillWARE. PACS: 44; 61; 81; 83; 89
INTRODUCTION
The variation of the melt temperature distribution in the cross sectional area of pipes has a significant impact on the cooling process and the final product quality [1]. The melt temperature variation in circumferential direction lead to ovality and non-uniform pipe wall thickness distribution. The extrusion time dependent respectively the axial melt temperature variation causes geometrical variations in extrusion direction.
These effects are well known in the plastic pipe production industry. This paper will introduce an analytical method to quantify the mentioned quality problems under the assumption of a known melt temperature distribution during entering the pipe vacuum calibration unit. The cooling simulation software chillWARE® is used to realize the relevant simulations.
The analysis is employed for a PE100 pipe with an outer diameter of 250-mm and a wall thickness of 24-mm (SDR1 10.4 is ratio of diameter to wall thickness). The pipe material is a standard PE 100 material.
CAUSES OF WALL THICKNESS VARIATION
It should be noted that non-uniform melt temperatures is only one of several possible causes of wall thickness variation. Overeijnder lists [8] the following possible causes.
-
Variations in elastic stresses in the melt caused by the folding of the polymer melt in the channels of a twin screw extruder – this is typical for RPVC.
-
Incorrect design of the flow channel of the extrusion die can destabilize the melt flow, creating waves in the pipe.
-
Incorrect temperatures of oven and screw can create temperature differences that influence the discharge of the melt from the screw channels. In this case, wall thickness variation is related to screw speed.
Proceedings of the Regional Conference Graz 2015 – Polymer Processing Society PPS
AIP Conf. Proc. 1779, 030005-1–030005-7; doi: 10.1063/1.4965475
Published by AIP Publishing. 978-0-7354-1441-9/$30.00
-
In multi-layer pipe extrusion viscosity differences between the layers can cause flow variation. This is referred to a wave instability or interfacial instability.
-
In some operations unmelted polymer particles reach the discharge end of the extruder. These can create waviness in the pipe.
-
It is possible that the frictional force of the melt against the calibration sleeve is greater than the melt strength – this causes velocity variation. This problem is more likely to occur in thin-walled pipe; it is sometimes referred to as slip-stick in the calibration sleeve. This problem can also occur with improper alignment between the extrusion head and calibrator.
-
In some situation the cleats of the puller do not have enough traction on the pipe causing slipping. This can create ring-shaped waves in the pipe.
-
In the extrusion of foam pipe the inner wall can become irregular when the cell sizes become too large (>
0.15 mm). This is sometimes referred to as the orange peel effect.
The wave amplitude typically varies from 0.1 to 3% of the wall thickness. The wave length varies significantly. The wave length is smaller than the wall thickness for items 2, 5, and 8. The wave length is about equal to the wall thickness for items 1, 4, and 6. The wave length is greater than the wall thickness for items 3 and 7.
MELT TEMPERATURES IN EXTRUDERS
Melt temperatures in extruders are the result of viscous dissipation and heat transfer. Conductive heat transfer is slow because polymers have very low thermal conductivity – about one hundred times lower than the thermal conductivity of steel. If we consider the metering section of a single screw extruder filled with molten polymer, the heat transfer in the melt close to the barrel surface is relatively efficient. As a result, the thin melt layer at the barrel surface can cool down quickly [6]. However, heat transfer in the melt further away from the barrel surface is inefficient because the low thermal conductivity.
The resulting melt temperature distribution is inherently non-uniform as shown in Figure 1 [6, 7]. This figure shows the melt temperature distribution in a 63.5-mm extruder running a fractional melt (0.2 gr/10min) HDPE at a screw speed of 100 rpm.
FIGURE 1: Melt temperature distribution in 63.5 mm extruder
Figure 1 is a color contour plot of the melt temperature distribution in a cross section of the screw channel in the metering section of the screw where the channel is completely filled with molten polymer. The channel depth has been magnified by a factor of eight to show the temperature distribution more clearly. It is clear that the melt temperature differences can be quite large. Unfortunately, these melt temperature differences are inherent to the polymer extrusion process.
Non-uniform melt temperatures in the screw channel result in temperature variation in the melt flowing through the die and in the melt emerging from the die. One of the results of these non-uniform melt temperatures is dimensional variation in the extrudate. This can happen in any extrusion operation. In this paper we will focus on pipe extrusion. In pipe extrusion the dimensional variation resulting from non-uniform melt temperatures is typically a waviness of the internal diameter. The outside diameter generally does not vary significantly because calibration results in a smooth OD of the pipe.
Melt temperature variation has been studied in detail at the University of Bradford, England [9-11]. Figure 2 shows melt temperatures measured with a wall thermocouple, a thermocouple mesh, and infrared.
FIGURE 2, Melt temperature vs. time comparing thermocouple mesh to infrared, courtesy University of Bradford
This figure shows that the wall thermocouple does not react significantly to melt temperature variation. The thermocouple mesh shows significant variation (10-20°C) at screw speeds of 70 rpm and higher. The melt temperature variation increases with screw speed. The infrared measurement shows significant variation at all screw speeds. At 90 rpm the IR temperature variation ranges from 20-25°C.
CHILLWARE® COOLING SIMULATION
The chill
WARE® cooling simulation software enables the possibility to simulate the cooling process of extruded pipes, sheets, films and profiles. The cooling situation can be analysed during the whole cooling process at arbitrary process positions. In addition to the pure temperature distributions in the pipe cross sectional area, residual stresses and thermal shrinkage are simulated as well. For exemplary applications of the software can be referred to [3], [4] and [5].
The outer diameter and the wall thickness changes during the cooling process. This behaviour is caused by the change in the material density as exemplary shown in Figure 3 for a reference PE100 material. The thermal density change generates a volume shrinkage of the material during the cooling process. The measurements in Figure 3 show a volume shrinkage of 23% during the cooling process. The volume shrinkage is separated in the radial, axial and tangential direction, whereas the distribution depends on the material, the SDR-class and the processing velocity. Of course, the absolute values for the change in geometry (outer diameter and wall thickness) depend on the melt temperature. Further information concerning the temperature dependent material properties can be obtained from [2].
FIGURE 3: Variation of the material density with changing temperature for different pressures for a PE100 material. The crystallization process can be observed in the region around 120°C.
The cooling simulation chill
WARE® is based on the finite difference and finite elements method and calculates the temperature distribution in radial pipe layers within the entire cooling section. The material properties of the polymers, such as the temperature-dependent thermal conductivity or the crystallization behaviour, have a major importance for the modelling. By adjusting a variety of parameters (e.g. coolant temperature, production rate or details of the cooling section) the optimal operating point of the cooling section can be determined. In the software the user-defined target internal temperature of the plastic products is used as a target value at a defined position in the cooling section.
INFLUENCE OF THE MELT TEMPERATURE ON THE FINAL PRODUCT GEOMETRY
The pipe geometry is mainly defined by the melt temperature, the mass throughput, the extrusion die geometry, the outer vacuum calibration and the vacuum and temperature settings in the downstream cooling sections. The major impact on the final outer pipe diameter is realized by the vacuum calibration unit (example shown in Figure 4). A perfect vacuum calibration realizes a full contact between the pipe outer surface and the inner calibration surface, which leads to an optimal heat transfer and a freezing of the outer pipe surface. Therefore the pipe outer diameter is restraint-guided until the pipe leaves the calibration. The calibration time depends on the calibration length and the processing velocity and is usually not sufficient to realize the required final cooling. Therefore, additional cooling sections (e. g. (vacuum) spray cooling tanks, immersion baths) are following behind the calibration. The temperature levels and distribution inside the pipe wall after leaving the calibration has a significant effect on the final product geometry. Usually, it is not possible to compensate occurring melt temperature variations in the calibration, so that a non-uniform melt temperature distribution at the extrusion die leads to a non-uniform pipe temperature distribution after the calibration.
FIGURE 4: Example for an adjustable and conical vacuum calibration (source: CCA GmbH)
EXEMPLARY SIMULATION OF GEOMETRIC VARIATIONS CAUSED BY NONUNIFORM MELT TEMPERATURE DISTRIBUTIONS
The effect of melt temperature variations on the product geometry is analysed exemplary with the simulation software chillWARE®. The reference production parameters are shown in Table 1.
Table 1: Process parameters applied for the simulation of the reference process
Parameter |
Unit |
Value |
Material |
- |
PE 100 |
Final Outer Diameter |
mm |
250 |
Final Wall Thickness |
mm |
24 |
Mass Throughput |
kg/h |
350 |
Melt Temperature |
°C |
218 |
Processing Velocity |
m/min |
0.35 |
Outer Diameter of Calibration |
mm |
256.6 |
Wall Thickness @ Extrusion Die |
mm |
31.04 |
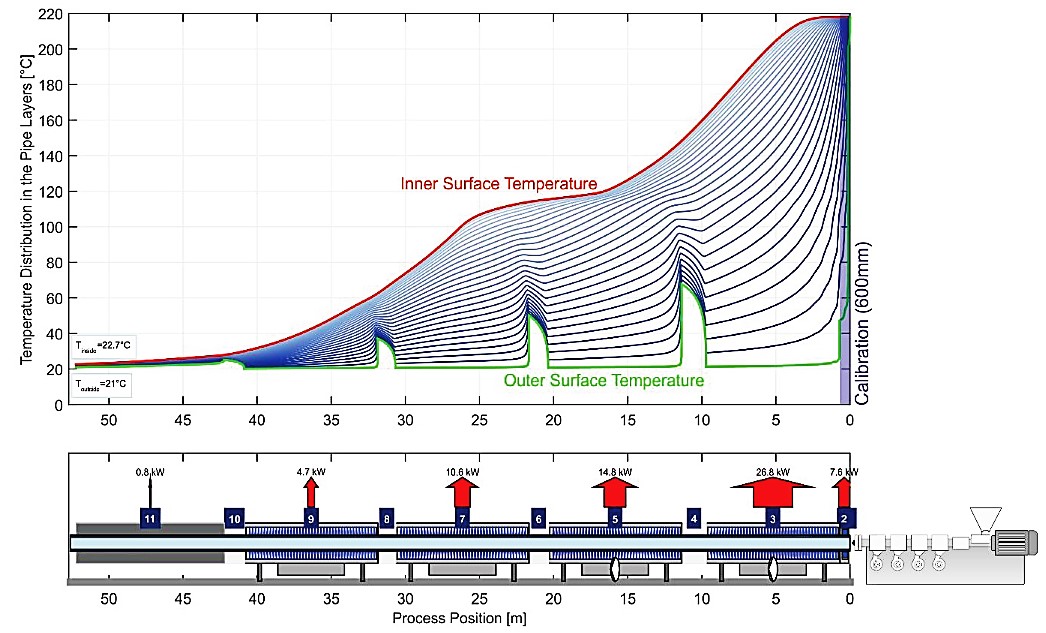
FIGURE 5: Cooling process for the reference production process. 7.6 kW thermal power is dissipated in the vacuum calibration unit. The outer surface temperature is 47.4°C, the inner temperature is still at 218°C melt temperature. The average cross sectional temperature is 194°C.
The cooling section contains a vacuum calibration with a length of 600mm, two vacuum spray cooling tanks with a length of 9000mm each and two spray cooling tanks with a length of 9000mm each. The cooling process as a result of the chill
WARE® simulation is shown in Figure 5.
The cross sectional temperature distribution at the end of the calibration is shown in Figure The outer diameter of the pipe experiences a thermal shrinkage of 3.5% from the extrusion die until the final product is finished at the end of the production line. The amount of thermal shrinkage depends on the melt temperature. The melt temperature is virtually decreased from 218°C down to 188°C in order to simulate variations in melt temperature. It is assumed, that the polymer volume flow rate remains unchanged.
FIGURE 6: Cross sectional temperature distribution at the end of the calibration for the reference process (homogenous melt temperature of 218°C at the extrusion die). The temperatures of the inner pipe layers are still near the melt temperature.
The corresponding simulation results directly after the vacuum calibration are presented in Figure 7. The average temperature is decreased from 194°C to 167.7°C. The outer diameter is fixed in the calibration; the thermal shrinkage of the outer diameter is reduced because of the lower average temperature level and the lower outer surface temperature. The dissipated thermal power is reduced from 7.6kW to 6.7kW due to the lower overall temperature gradients. Most interesting is the simulation of the resulting change in the outer diameter. The reference cooling process (cooling units and cooling fluid temperature levels) is unmodified and optimized for a target outer diameter of 250-mm and a wall thickness of 24-mm. The simulation results show, that the final product outer diameter is enlarged from 250.00-mm to 250.99-mm (+1,004%) and the pipe wall thickness is scaled up to 24.54mm (+1,022%). The geometric changes can be compensated by adapting the vacuum level in the first spray cooling tank or modifications in the calibration, if an adjustable calibration is available. This is only possible for a continuous/stable change in the melt temperature. This is usually not the case, if the changes in the melt temperature are a result from phenomena in the screw extruder.
FIGURE 7: Cross sectional temperature distribution at the end of the calibration for the modified process (melt temperature decreased to 188°C at the extrusion die). The average temperature of the pipe cross section is reduced from 194.0°C to 167.7°C
An example for a resulting waviness in the product surface (change of the outer pipe diameter) is shown in Figure 8. The introduced reference process and the modified variant are applied, the melt temperature variation occurs with a frequency of
f 0.833
Hz which correspond to an extruder RPM of Z 50
U /min . The resulting time dependent outer diameter
Da(
t) is calculated with the reference outer diameter
Da,ref 250
mm , the enlarged diameter
Da,mod 250.99
mm to
Da (t) 0.5((Da,mod Da,ref )sin(2S f t) Da,mod Da,ref ) . (1)
FIGURE 8: Resulting sinusoidal variation in the pipe surface (outer diameter) caused by a non-uniform melt temperature.
SUMMARY AND CONCLUSION
The effect of non-uniform melt temperatures on the geometry of a pipe with outer vacuum calibration is analysed in this contribution. The cooling simulation software system chillWARE® is employed to quantify the resulting variations of the outer pipe diameter and the wall thickness for a PE100-pipe with an outer diameter of 250mm and a wall thickness of 24mm (SDR 10.4). Melt temperature variation of 30°C (188°C-218°C) is applied as initial conditions for the simulation. Most important for the final product geometry is the cooling process in the outer vacuum calibration and the subsequent thermal shrinkage caused by the temperature dependent density of the thermoplastic material. The simulation results show that the outer diameter is increased by 1.004% and the pipe wall thickness enlarged by 1.022%. Furthermore, the generation of a wavelike product surface for and screw extruder driven with 50 rpm is calculated based on the simulation results. This contribution shows the importance of a stable thermal control of the melt temperature in order to guarantee an adequate product quality. Non-uniform melt temperatures can cause essential problems regarding the final product geometry and surface quality.
REFERENCES
-
M. del Pilar Noriega E. and Chris Rauwendaal: Troubleshooting the Extrusion Process, Hanser Publisher, Munich, 2005.
-
Menges, Haberstroh, Michaeli: Werkstoffkunde Kunststoffe, Carl Hanser Verlag, 2011
-
Hiesgen, Saul, Spitz, Weiss: Pipe cooling simulation for energy savings and enhanced product quality, Proceedings of the Polymer Processing Society 28th Annual Meeting ~ PPS-28 ~ December 11-15, 2012, Pattaya (Thailand)
-
Hiesgen, Saul, Spitz, Weiss, Wortberg: Application of the finite difference method for the cooling process simulation of multi-layer pipes and cables, Proceedings of the Polymer Processing Society 29th Annual Meeting ~ PPS-29 ~ July 15-19, 2013, Nuremberg (Germany)
-
Weiss, Hiesgen, Saul, Spitz: Cooling simulation for the prediction of quality properties and production costs of semi-finished extruded products like pipes, Plastics Engineering, June 2014 & SPE ANTEC 2014, 29th of April, Las Vegas, Nevada, USA
-
Rauwendaal, Chris: Leakage flow in extruders, Ph.D. thesis Twente University (the Netherlands) December 1988
-
Rauwendaal, Chris: FEA of flow in single screw extruders, 52nd SPE ANTEC, 298- 305, San Francisco, CA, co-author Jeff Anderson (1994)
-
Overeijnder, Hans: PVC processing with counter-rotating twin screw extruders, Extrusion seminar Twente University, February 2-4, 2015
-
Kelly et al.: Melt temperature field measurement in single screw extrusion: influence of melt pressure and die geometry, SPE ANTEC, p.291-295, 2005
-
Sorroche et al.: Thermal optimization of polymer extrusion using in-process monitoring techniques, Applied Thermal Engineering, Volume 53, Issue 2, May 2, 2013, Pages 405–413
-
Sorroche et al.: Infrared melt temperature measurement of single screw extrusion, Polymer Engineering & Science, May 2015