
Polyethylene fittings production factory
The producer of polyethylene pipes and fittings
Polyethylene fittings production factory could be in different conditions, based on the fitting types it produces. But regardless of the fittings being produced, the factory environment has to be clean, neat and fully optimized and safety tips should be applied so the safety of machines’ operators would be ensured. In polyethylene fittings production factory, some place for storing the raw material should be foreseen that the raw material would be stocked there safely and in order.
A fittings production factory would better have obtained the work health certificate of ISO 18001 and environmental certificate of ISO 14001 according to the latest versions of the international organization for standardization (ISO) from a credible institution, and also the HSE regulations have to be observed in the workplace.
If the production lines of polyethylene fittings were made from materials into which the granule materials of polyethylene should enter as the raw material, there has to be silos beside the production lines and machines for storing the raw material needed for feeding to the machines.
The factories producing fittings, do also produce a large amount of polyethylene waste products especially the producers of injective fittings and also machined fittings such as polyethylene flanges which are trimmed from a molded sheet. Inside the factories, there must be places for storing and segregating of the waste products so that such wastes do not get mixed with the final and approved product and the product would be 100 percent reliable.

The factories producing injective fittings put the injection machines in a row and lead the feeding machines’ raw material pipes toward them via silos. In this method, the polyethylene granules are used as the raw material. High pressure injective fittings (up to 250 bars), twisting polyethylene fittings and electrofusion fittings are all produced by the injection machines.
Polyethylene pipes are used as the raw material in the factories producing mitering fittings and custom fittings. Namely, first the polyethylene pipe is divided into required pieces and finally welded with different polyethylene welding machines and the desired fittings are made. The fittings made via mitering method would be the best type of polyethylene fittings if they were made from the very material of polyethylene pipes used in the project and they would reveal high resistance in comparison to the pipes.
The factories producing polyethylene fittings must contain quality control laboratories where should have 17025 Certificates and other required certificates and make use of suitable and up to date equipment and also trustworthy and well aware technicians.
A fitting producing factory is not only limited to manufacturing and testing of the product, but also includes packing and transporting the polyethylene fittings to the customers and project site which is of the most important parts. The fittings have to be packed in a way that prevents collisions between them and the loading must be done cautiously so that the outer body and edges would not get damaged and the packing be in boxes if possible. Tiny injective fittings and twisting fittings are packed in the boxes which is suitable and safe, but about mitering fittings, big and high pressure custom fittings, there will be no proper packing available. Big polyethylene fittings and the fitting ends are wrapped by bubble wraps and taped and put regularly on wooden or plastic pallets as much as possible, then they are belted to stay fixed.
Important note: buy your fittings from a factory or manufacturer who produces both the polyethylene pipes and fitting and not only one of them.
Polyethylene mitering and welding fittings

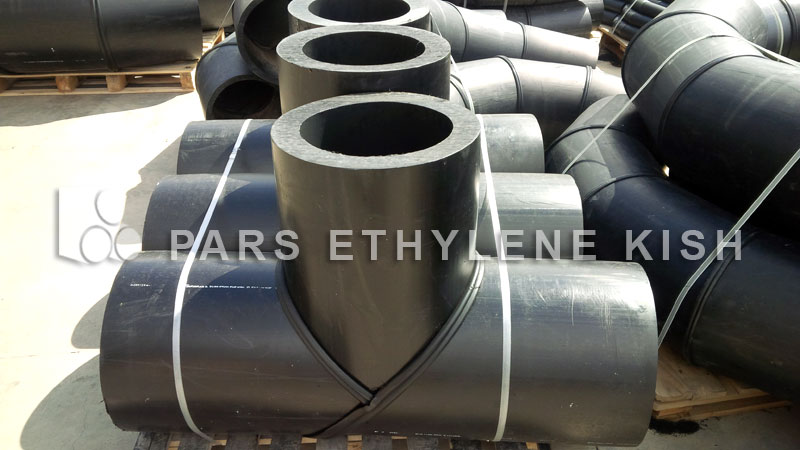



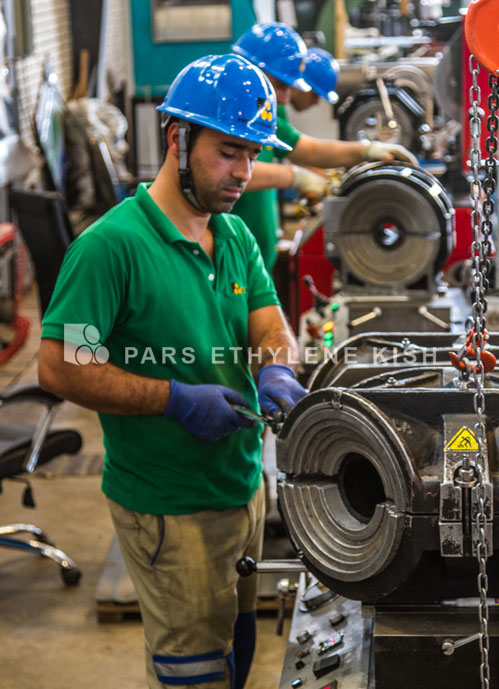
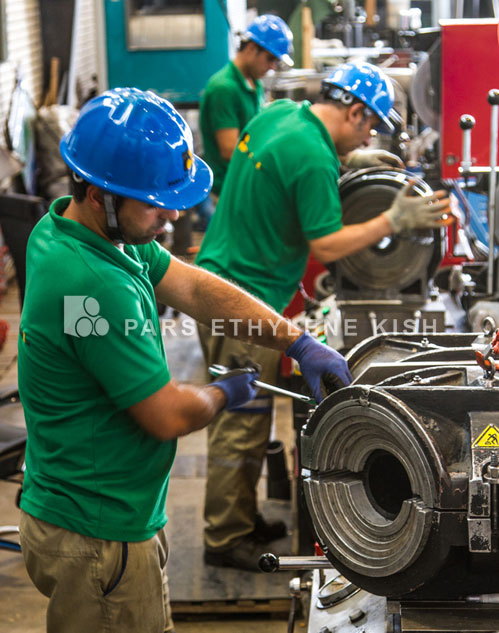
