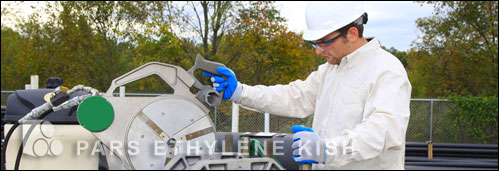
Polyethylene Welding Machine
HDPE pipe fusion machine - Butt Fusion Device
HDPE pipe fusion machines is one of the products of Pars Ethylene Kish for connecting pipes and fittings of polyethylene.Polyethylene pipe welding machine and their fittings are available in two models of the bottle fusion and electrofusion, each of which has its own uses and advantages that are selected and used relative to the project's (pipeline) size and size of pipe and fittings.The polyethylene butt fusion welding machine is the most used with the same butt welding device, and these devices are produced and supplied in twenty-five different models, from 110 to 2400 mm, and capable of welding up to a pressure of 40 atmospheres. Pars Ethylene Kish welding Machine is based on Standard 12176ISO and the standard 2201DVS. This company's polyethylene welding machine is designed to be unique for carrying out work on site and workshop environment.
Polyethylene pipe welding machines are manufactured using the best quality raw materials available on the market, and the company's polyethylene welding machines are certified by the inspectors of the water supply and power plant, and all products with warranty and after service sales are offered. These welding machines are tested, calibrated after producing.
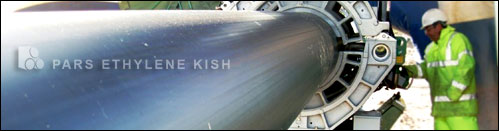
Boiling Butt Performance
The molecular structure of the polyethylene pipe changes to the amorphous (shapeless) state of the heat, resulting in the tube becoming a flexible material. After boiling and cooling, the weld location and the molecular structure change from amorphous to crystalline, and thus the joints are uniformly matched to the polyethylene pipe.
Various kinds of polyethylene pipe welding machine
Polyethylene pipe welding machines are divided into three general models, each of which uses different types and advantages, and each of them depends on the application of the pipeline, requirements, connections and project conditions.
1- Butt fusion machine (Butt-boil)
Welded fittings of the butt of the polyethylene pipe can be used in water supply and sewage systems and their distribution network, fire extinguishers under different pressures. This kind of welding, if properly done, is the best method for connecting in a polyethylene tube with polyethylene joints. In welded joints, the welding quality and its efficiency depends on the skill and ability of the welder, the suitability and proper performance of the welding machine and related equipment, and the observance of the principles and rules of welding.
It is recommended to read the guide for welding pipe and fittings of polyethylene.
Various types of butt fusion tubes for polyethylene pipes
-
- Double-jaw welding machine
-
- Manual hydraulic welding machine
-
- Electric hydraulic welding machine
-
- Angled Welding Machine
The sizes of the butt welding fusion tube and the polyethylene fittings
-
- sewege 50 -160mm Polyethylene pipe welding machine
-
- 63 - 250mm Hydraulic and manual polyethylene tube welding machine
-
- 90 - 250mm Polyethylene Hydraulic Pipe Welding Machine
-
- 90 -315mm Polyethylene Hydraulic Pipe Welding Machine
-
- 400- 200mm Polyethylene Hydraulic Pipe Welding Machine
-
- 250 - 500mm Polyethylene Hydraulic Pipe Welding Machine
-
- 315 - 630mm Polyethylene Hydraulic Pipe Welding Machine
-
- 710 - 1200mm Polyethylene Hydraulic Pipe Welding Machine
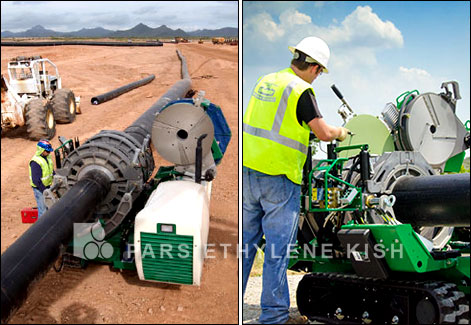
2- Electrofusion welding machine
Electrofusion welding joints are commonly used in gas distribution networks to connect polyethylene pipes to each other. Use of this type of fittings according to the recommendations of the standard of the National Iranian Gas Company and DIN of Germany to achieve the highest yield. The use of a suitable and specific tool for the success of electrophysitic welding is essential. It is always advisable to check all the necessary equipment before starting welding. Make sure all the equipment that needs calibration are calibrated. The equipment may be somewhat varied depending on the product under welding or the diameter to be welded. Electrofusion is suitable for pipes of 16 to 710 mm, while a fusion butt can be used for pipes of 50 to 2000 Mm. In the case where the polyethylene pipe must be installed using a drilling technique such as a drill bit, then no Electrofusion can be used. Similarly, if the tube should be used as a tight cover in an existing pipeline, the fusion butt is the only technique.
It is recommended to study electrofusion welding training
Features of Electrofusion Welding Machine
-
1 - Non-welding in electricity orders
-
2 - Increased connection integrity
-
3 - Automatic control
-
4 - Reduction of human error in welding due to welding parameters by the device
-
5 - Compatibility between electrofusions and other electrofusion systems via computer barcode system
-
6 - Ability to use for pipes and fittings up to 1200 mm in size for use in water and gas
-
7 - Ability to connect to the printer and connect to the computer
-
8 - Voltage and frequency of input power display feature
-
9 - Low weight of welding machine
3- Extruder welding machine
Extruder welding machine is used to repair the connections of the polyethylene pipe as well as welding them. This type of device is produced in a variety of sizes and types. The extruder welding machine is used manually to repair polyethylene pipe welding.
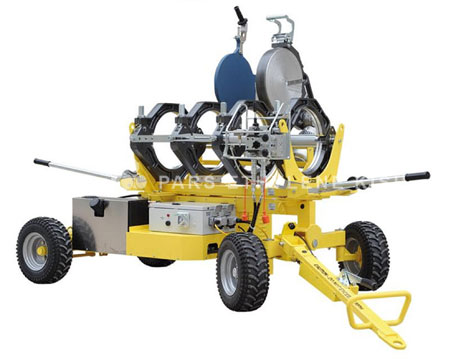
Components of polyethylene tube welding machine
-
1 - The main chassis of the machine with the corresponding clamps to the desired size of the device
-
2 - Hydraulic unit of the machine with electromotor and hydraulic pump
-
3 - Grate plate with electro-motor and gearbox
-
4 - Hot plate of all non-stick Teflon with element
Accessories for polyethylene tube welding machine
-
- Double-sided electric grate with linear drills and bearings
-
- Electric heater with main elements
-
- Spring box for storing adapters
Pars Ethylene Kish welding machines have been designed and manufactured according to the latest designs of the world. With a standard spring and main bearings, the speed and precision of welding of sewage pipes of 45, 90, 90, and knees are done.
Steps of welding the polyethylene pipe
Pipes and fittings of polyethylene are usually made using a Butt Fusion method in this way:
-
1 - First, the tube is placed in the two jaws of the welding machine (fixed and movable) and after the necessary adjustments, the molds are closed.
-
2 - The grate plate is placed between the two tubes and finishes the edges of the tubes thoroughly and cleaned and then removed.
-
3 - Place the hot plate, which has reached the permitted temperature (210-220 ° C), between the tubes and the two tubes are attached to it and the pressure is raised according to the instructions of the welding machine.
-
4 - We continue to heat under pressure to make the pipes in contact with the hot plate, circular and uniform of the specified size.
-
5 - In the above step, the pressure decreases and the internal layers are melting at the joint.
-
6 - The moving part of the welding machine is pushed back and the hot plate is separated so that no harm is caused to the melting surfaces.
-
7 - The two ends of the tube are quickly fastened together and the pressure is gradually increased and kept constant until the boiling point is cooled.
-
8 - The cooling time in the above step depends on the thickness of the pipe and fittings.during this time, the joint must not be exposed to stresses with unacceptable pressure.
-
9 - The welding edge at the joint must be in a two-piece bundle. The formation of this lump indicates that the welding is done uniformly.
Detailed methods and training are provided in the specialist sections. The welding process of polyethylene pipe and joints must be carried out by qualified people with a certificate to ensure the weld quality.
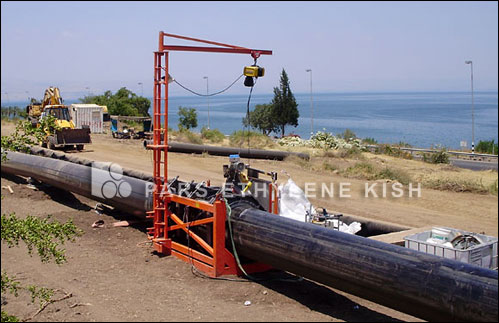
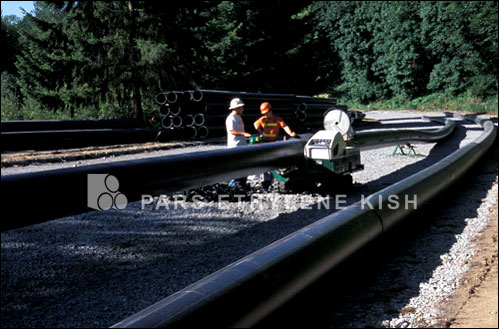
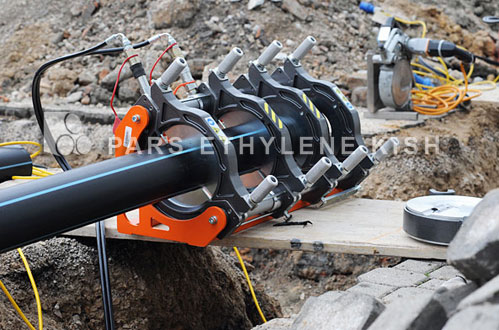
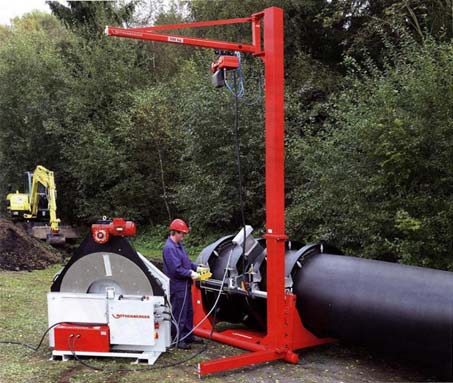
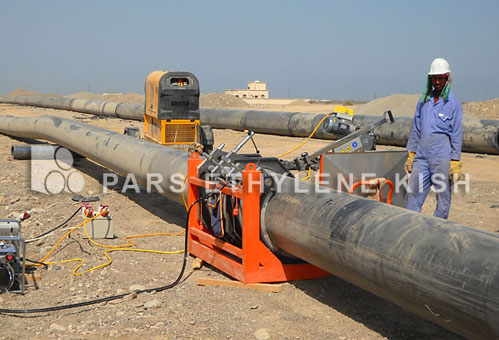
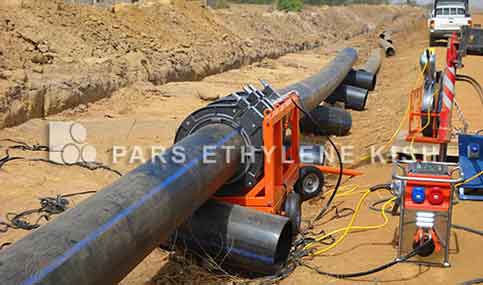