What is polyethylene pipe welding?
Polyethylene pipe welding may not seem like the most glamorous topic, but its impact on our daily lives cannot be overstated.
From delivering clean water to our homes to ensuring the safe transport of gas and other materials, PE pipes are an essential component of our modern infrastructure.
The process of welding these pipes together is a fascinating blend of science and art, requiring precision, skill, and specialized equipment.
So let's take a closer look at the world of polyethylene pipe welding and discover the innovation and creativity behind this vital process.
What is it?
Polyethylene (PE) pipe welding is a process of joining two sections of PE pipes together by melting and fusing the ends of the pipes using heat and pressure. PE pipes are commonly used for water supply, gas distribution, and other industrial applications.
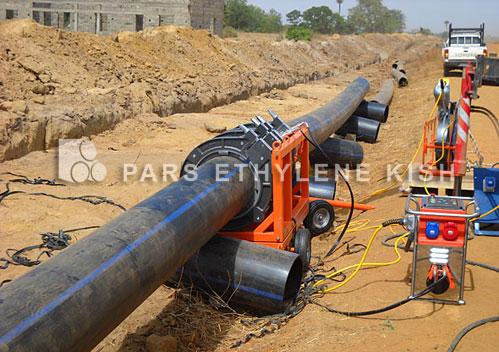
There are two common methods for PE pipe welding: butt fusion and electrofusion.
Butt fusion welding is the most widely used method for joining PE pipes. This method involves heating the ends of two pipes simultaneously to a specific temperature (generally around 200-220°C) using a specialized butt fusion welding machine. Once the ends of the pipes reach the desired temperature, they are brought together and held under pressure until they cool and fuse together. The result is a strong and permanent joint.
Electrofusion welding is a method that uses an electric current to heat a wire coil embedded in the fitting, which in turn heats the end of the pipe. The heat generated by the current melts the plastic material, and the molten plastic is then allowed to cool and fuse the pipe and fitting together.
Both butt fusion and electrofusion welding require specialized equipment and training to ensure a proper and durable joint. It is important to follow the manufacturer's guidelines and industry standards when welding PE pipes to ensure a safe and reliable pipeline.
Is polyethylene pipe welding expensive?
The cost of polyethylene pipe welding can vary depending on several factors such as the size of the pipe, the type of welding method used, the equipment required, and the expertise of the welder. Generally, butt fusion welding, which is the most common method used for PE pipe welding, requires specialized equipment such as a welding machine, heating plate, and clamps. The cost of these machines can range from a few hundred to several thousand dollars, depending on their size and complexity. Electrofusion welding equipment is typically less expensive, but the cost of the fittings can be higher.
In addition to the equipment costs, the cost of labor is also a significant factor. Polyethylene pipe welding requires skilled and experienced welders who are trained to follow strict safety and quality standards. The cost of hiring a professional welder can vary depending on their experience and location.
Overall, the cost of polyethylene pipe welding may be considered relatively high compared to other types of pipe joining methods. However, it is important to note that the long-term benefits of a properly welded PE pipe system, such as increased durability and reduced maintenance costs, often outweigh the initial investment.
What are the best types for it?
There are several types of polyethylene (PE) pipes and fittings that are suitable for welding. The most commonly used types include:
-
HDPE pipes are the most widely used type of PE pipes for welding. They are known for their high strength, durability, and resistance to chemicals and abrasion, making them ideal for applications in water supply, gas distribution, and industrial piping systems.
-
MDPE pipes are also suitable for welding and are often used for gas distribution systems. They are slightly less dense than HDPE pipes and are generally less expensive.
-
PP pipes are another type of thermoplastic pipe that can be welded. They are known for their high chemical resistance and are often used in industrial applications.
-
Electrofusion fittings are specially designed fittings that can be used to join PE pipes using electrofusion welding. These fittings are available in a variety of shapes and sizes, making them suitable for a wide range of applications.
In general, it is important to select the appropriate type of PE pipe and fitting for the specific application and ensure that the welding process is done according to industry standards and manufacturer guidelines.
The best pipe factory for polyethylene pipes in the middle east, Pars ethylene-kish
Welcome to our state-of-the-art polyethylene pipe factory Pars ethylene-kish, where innovation and quality meet to create the best piping solutions for your needs. Our factory boasts the latest technology and equipment, manned by a team of skilled professionals who are passionate about their craft.
From raw materials to finished products, our production process is meticulously monitored to ensure the highest quality standards are met. We use only the best materials, such as high-density polyethylene and polypropylene, to create pipes that are strong, durable, and resistant to corrosion and wear.
Our pipes are designed to meet the demands of a wide range of industries, including water supply, gas distribution, telecommunications, and industrial piping systems. We offer a variety of pipe types and sizes, as well as fittings and accessories to suit your specific needs.
At our factory, we understand the importance of sustainability and the impact that our manufacturing processes can have on the environment. That is why we use eco-friendly and energy-efficient methods to reduce our carbon footprint and minimize waste.
We take pride in our commitment to customer satisfaction and strive to provide the best service possible. Our knowledgeable and friendly staff are always available to answer any questions you may have and help you find the perfect solution for your piping needs.
Choose our imaginary pipe factory for high-quality, durable, and sustainable piping solutions that meet your exact requirements.
Final thoughts on polyethylene pipe welding
In conclusion, polyethylene pipe welding plays a critical role in our modern infrastructure, providing reliable and durable piping solutions for a wide range of applications. Whether it's for water supply, gas distribution, telecommunications, or industrial piping systems, the welding of PE pipes requires specialized equipment, skilled professionals, and strict adherence to safety and quality standards.
While the cost of PE pipe welding may be relatively high compared to other joining methods, the long-term benefits of a properly welded system, such as increased durability, reduced maintenance costs, and improved safety, often outweigh the initial investment.
As the demand for efficient and sustainable piping solutions continues to grow, the importance of polyethylene pipe welding will only continue to increase. With advancements in technology and a growing focus on sustainability, we can expect to see further innovation and improvements in the welding of PE pipes in the future.