
Equipment for production line of polyethylene pipes and connections
Production line of HDPE Pipe
Production line of polyethylene pipes and connections o Pars Ethylene Kish company consists of the most developed and new technologies and equipment for production of polyethylene pipes and connections throughout the world. These devices are all made in Germany. Pars Ethylene Kish company has been able to raise the quality level of its productions up to the international standards and claim itself as a serious rival for the foreign products in the Middle East region.
the production lines of polyethylene pipes comprise of different machineries which are classified into machineries located at the beginning of the line and end of the line. All this equipment on the production line of polyethylene pipes are of high importance and each play a role which finally influences the quality of the final product and almost all of them are necessary.
The equipment and machinery for production line of polyethylene pipes are as follows :
The suction machine is responsible for taking the raw material of poly ethylene in as required and getting them to the funnel and extruder machine entrance.
The Gravimetric is installed on the entrance funnel of the extruder and is responsible for automatic controlling of weight and quantity of the raw material used in the production of polymer (poly ethylene, Polypropylene, etc.) pipes while producing oxygen in the extrusion lines.
Extruder is the heart of the production line of polyethylene pipes in which the extruder machined are used for initial shaping of polymer pipes for the next operations and also for shaping of the final products.
All machines include monitoring and operation control systems on them but there is this possibility that all of them would be controlled in harmony by the control system of the extruder.
Die (die head) is the conduit between the die head and extruder which raises the pressure behind the die (end of cylinder) compresses the melted materials and uniformly distributes them into the die head entrance to ensure stability and quality status of the product.
Vacuum tank is located after die hard and before cooling tanks. The melted poly ethylene materials which are in paste form after passing the die hard, have to pass the vacuum tank to get the initial form of poly ethylene pipes.
Ultrasonic is installed after the vacuum tank and is responsible for measurement of the pipes thickness from 8 different points.
The cooling tanks which are located at the middle of the production line of poly ethylene pipes, after the vacuum tank and before Hauloff and marker machines, are responsible for the final cooling of poly ethylene pipes. Their number is determined according to the production line speed and size of the produced pipes.
The hauloff machine has an important role which is to haul off the pipe regularly and uniformly without applying any extra pressure and its speed has to be in accordance with exit speed of the melted materials from the extruder and hence the pipe thickness would not be affected and also the pipe body would not be under much pressure which causes out-of-roundness.
Marking and inscription of the produced poly ethylene pipe specifications is what marker machine is responsible for. The marker machine inscribes the specifications of the pipe and production shift and date and also raw material type and standard number on the pipe. Marker machines are divided into two types: thermal and laser which the standard requires the thermal type, but in some cases and upon the customer’s request the jet printer is also used and the specifications of gas-specific polyethylene pipes are inscribed on the pipes using the jet printers.
Cutting the pipes into pieces with accurate measurement and smooth cutting edge is what the saw does. If only one the tip is to be considered while sawing, it would be that while sawing, the cutting blade has to in coordination with the exiting speed of the pipe, so that the line would not stop.
the pipes roll over the dock table or tilting after the cutter and are transferred to the storage from this table.
The production line of the polyethylene pipes up to size of 110 might include a winder at the end of the line for winding the pipes.
All the extruders used in the production of polyethylene pipes and connections of Pars Ethylene Kish company are made by the two German companies named Batternfeld and Batternfeld Cincinati which have the most advanced automatic control system while producing polyethylene pipes which prevents occurrence of any faults during production of polyethylene pipes and connections.
The production line of polyethylene pipes and connections in Pars Ethylene Kish company is one the most modern and accurate machines for polyethylene pipes and connections in the country which has managed to challenge the best poly ethylene products in the region and world in terms of quality.
Production line of single wall polyethylene pipes
Double wall polyethylene Corrugated Pipe production line
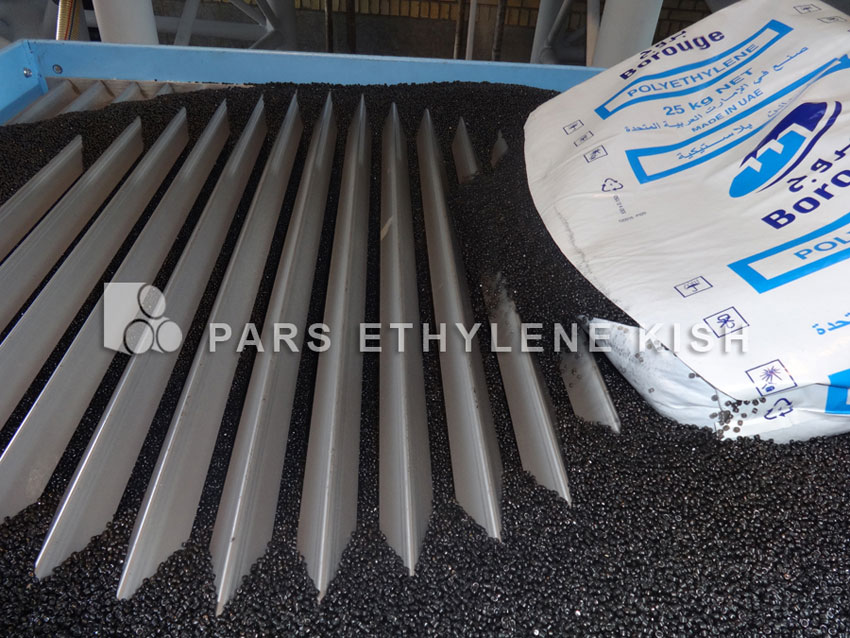
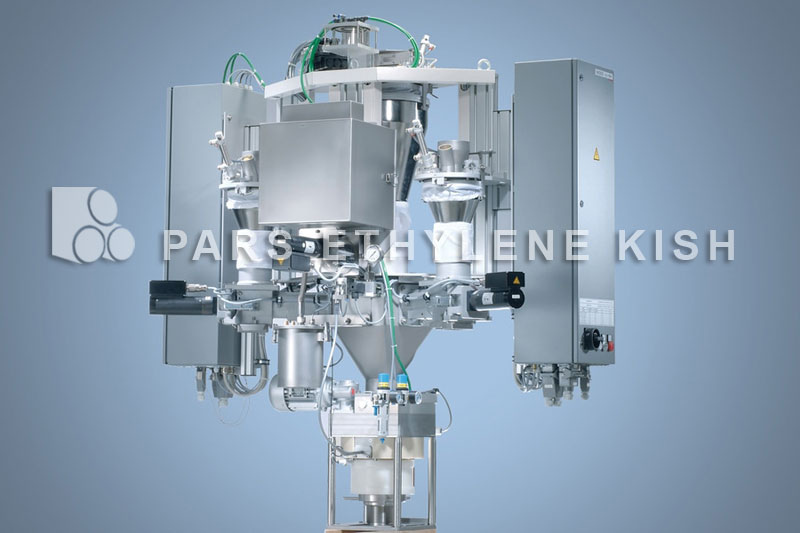


