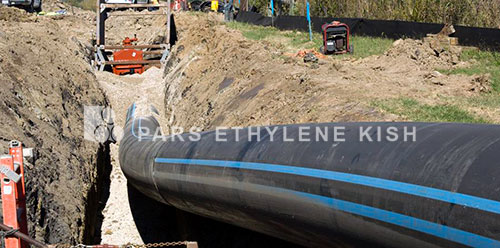
Installation Guidelines for PE Pipe
Install PE pressure pipe in accordance with ASTM D2774.
The engineer must evaluate the site conditions, the subsurface conditions, and the application objectives to determine the extent of support the pipe may need from the surrounding soil. Where the pipe burial depth is relatively deep, where subsurface soil conditions are not supportive of pipe, where surface loads or live loads are present, or where the pipe DR is high, the engineer will generally prepare a specific installation specification. The specific engineered installation instructions should be followed.
The following are general guidelines for the installation of 12” and smaller diameter PE pipe with a minimum cover depth of 2 ft (3 ft under traffic loading; up to 5 feet for frost protection) and a maximum depth of cover of 16 feet. For other depths consult the engineer. Other satisfactory methods or specifications may be available. This information should not be substituted for the judgment of a professional engineer in achieving specific requirements.
Trench Length
The length of open trench required for fused pipe sections should be such that bending and lowering the pipe into the ditch does not exceed the manufacturer ’s minimum recommended bend radius and result in kinking. Table 4 lists the recommended lengths of trench openings for placement of continuous lengths of fused pipe, assembled above the trench. When the trench sidewalls are significantly sloped, somewhat shorter trench openings may be used.

Trench Width
The trench width should allow sufficient room for joining the pipe, if required, snaking small diameter from side to side along the bottom of trench for thermal affects, and filling and compacting the side fills.Table 3 gives suggested minimum trench width values.

Trench Construction
Principal considerations in trench construction are trench width, length, and depth; soil stability; and groundwater accumulation in the trench. Unstable soils or wet conditions should be controlled by sloping or bracing the trench walls, de-watering the trench bottom, and/or other measures.
Placing Pipe in Trench
Place polyethylene pressure pipe up to 8” in diameter in the trench by hand. Use equipment to lift, move, and lower larger diameter pipe into the trench. Pipe must not be dumped, dropped, pushed, or rolled into the trench.
Optimal Burial Depth for Polyethylene Pipes
Polyethylene pipes have gained widespread popularity in various infrastructure projects due to their exceptional attributes such as durability, flexibility, and resistance to chemicals. Proper installation of these pipes is pivotal in ensuring the longevity, safety, and efficiency of the pipeline system. Among the crucial considerations in this installation process is determining the optimal burial depth. This comprehensive guide delves into the factors influencing the ideal burial depth for polyethylene pipes, adherence to local regulations, and the significance of this decision for different projects.
Factors Influencing Burial Depth for Polyethylene Pipes
Polyethylene pipes serve as critical conduits in diverse applications like water supply, gas distribution, and telecommunications. The depth at which these pipes are buried significantly impacts their structural integrity, thermal stability, and overall performance. Several factors contribute to the determination of the optimal burial depth for polyethylene pipes:
Environmental Conditions
The geographical region where the polyethylene pipes are to be installed holds a substantial sway over the appropriate burial depth. Elements such as average temperature, seasonal fluctuations, and groundwater levels play a pivotal role in this determination. In regions marked by high water tables or substantial rainfall, engineers are tasked with ensuring the pipes are buried at a depth that counteracts buoyancy-related issues. Failure to address these concerns may result in pipe uplift or displacement, compromising the functionality of the pipeline system.
Impact of Ground Traffic and Land Use
In urban locales or areas subject to high ground traffic, the potential for external loads on buried pipes necessitates meticulous evaluation. Transformations in land use, including new constructions or intensive operation of heavy equipment, can exert additional pressure on buried pipes. Thorough analysis of these factors enables engineers to ascertain the optimal burial depth and institute safeguarding measures. These measures can involve the incorporation of reinforced bedding materials to forestall damage to the pipes.
Pipe Diameter and Wall Thickness
The dimensions of polyethylene pipes, encompassing diameter and wall thickness, exercise considerable influence on the recommended burial depth. Pipes with larger diameters or thicker walls might demand greater burial depths to ensure stability and resistance against external forces. Manufacturers usually furnish guidelines outlining the maximum allowable burial depth for varying pipe specifications, which engineers must factor into their decisions.
Adhering to Local Regulations
Proper adherence to local building codes and industry standards constitutes a cornerstone in the successful installation of polyethylene pipes. These codes are established to safeguard public safety, environmental preservation, and the durability of infrastructure. Such codes often stipulate minimal burial depths, proper bedding materials, and other installation requisites for polyethylene pipes. These specifications are influenced by regional environmental conditions and engineering best practices.
Industry Guidelines
In tandem with local building codes, consulting industry guidelines and recommendations is paramount for engineers and contractors tasked with determining the ideal burial depth for polyethylene pipes. Esteemed organizations like the American Water Works Association (AWWA), ASTM International, and the Plastics Pipe Institute (PPI) provide invaluable resources concerning pipe installation and design. These resources encompass insights into proper burial depths for diverse pipe applications, further enriching the decision-making process.
Coordination with Utility Companies
For ventures involving utility pipelines, fostering collaboration with relevant utility companies assumes utmost importance. These utility companies often possess their own specifications and prerequisites for the installation of their pipelines. Effective coordination with these entities guarantees the proper placement and maintenance of all subterranean infrastructure, thereby minimizing conflicts and enhancing overall project efficacy.
Conclusion
The optimal burial depth for polyethylene pipes stands as a pivotal determinant in upholding the safety, longevity, and operational efficiency of the pipeline system. While the prevention of freezing is a primary concern in colder climates, safeguarding against surface-related threats takes precedence in warmer regions. Engineers and contractors, equipped with insights into factors like application, pressure rating, soil characteristics, environmental conditions, traffic loads, and local regulations, are poised to make well-informed decisions that yield dependable and enduring pipeline systems.
Polyethylene pipes retain their prominence across various applications due to their exceptional attributes. Realizing the full potential of these pipes hinges upon precise installation, with a icular emphasis on the selection of the appropriate burial depth. By adhering to industry best practices, collaborating with seasoned professionals, and conforming to local regulations, engineers can assure the successful installation and operation of polyethylene pipelines. These pipelines, facilitating critical functions such as water supply, gas distribution, and telecommunications, underscore their significance as vital components of essential infrastructure projects.
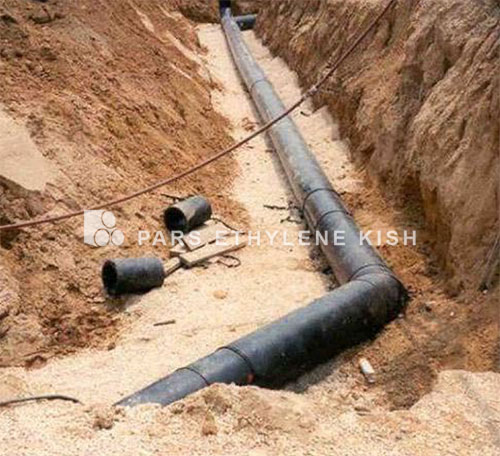
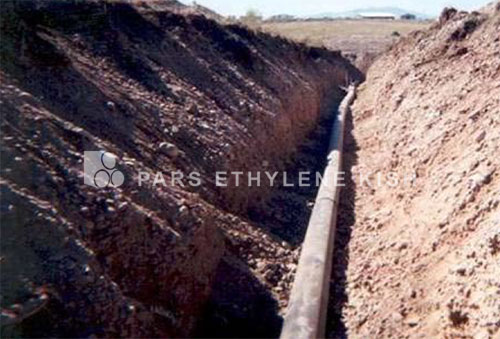
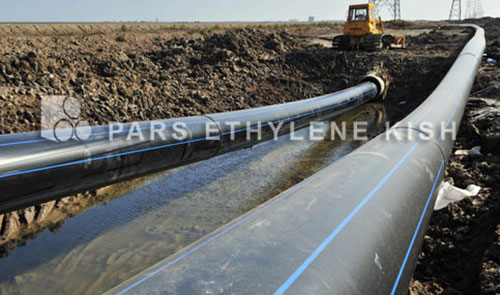
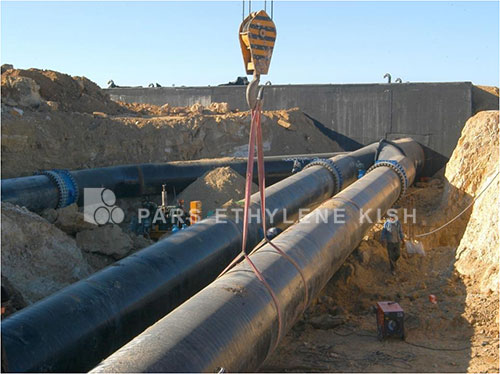
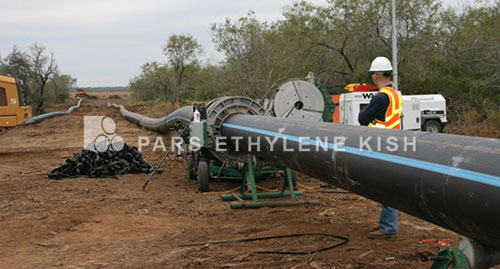