Polycarbonate
1. Introduction to Polycarbonate
Polycarbonate is a type of thermoplastic polymer that is widely used in various industries for the production of a wide range of objects. It is derived from the monomer bisphenol A (BPA) and phosgene gas. Polycarbonate is known for its exceptional properties, such as high transparency, impact resistance, lightweight nature, heat resistance, and electrical insulation capabilities. These qualities make it a versatile material with numerous applications in different fields.
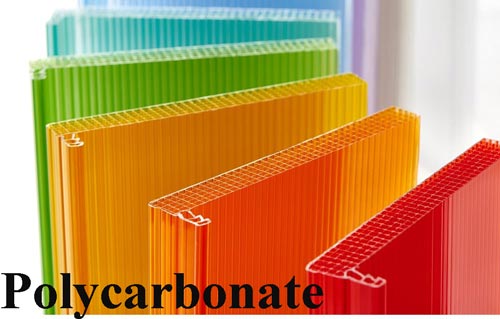
1.1 Definition and Overview
Polycarbonate is a synthetic polymer that belongs to the family of thermoplastics, which means it can be melted and reprocessed multiple times without undergoing significant chemical changes. It is characterized by its long-chain structure, composed of repeating carbonate units. Polycarbonate is known for its clarity, resembling glass, but with much greater impact resistance.
1.2 Manufacturing Process
The manufacturing process of polycarbonate involves the synthesis of the monomer bisphenol A (BPA) and its subsequent polymerization to form the polycarbonate polymer.
The first step in the process is the synthesis of bisphenol A, which is accomplished through a reaction between phenol and acetone. This reaction results in the formation of BPA, a key precursor for polycarbonate production.
The next step involves the polymerization of BPA. This is achieved by combining BPA with phosgene gas (COCl2). The reaction between BPA and phosgene results in the formation of polycarbonate polymer chains. The polymerization process can be controlled to achieve the desired molecular weight and properties of the polycarbonate.
Once the polymerization is complete, the polycarbonate is processed into various forms, such as sheets, pellets, or granules, depending on the intended application.
1.3 Properties and Characteristics
Polycarbonate exhibits a range of unique properties and characteristics that contribute to its widespread use in various industries:
Transparency and Optical Clarity: Polycarbonate is highly transparent, allowing for excellent light transmission. It possesses optical clarity similar to glass, making it suitable for applications where visibility or transparency is desired.
High Impact Resistance: One of the key advantages of polycarbonate is its exceptional impact resistance. It is significantly more durable than many other plastics, making it ideal for applications that require protection against impact or breakage.
Lightweight and Versatile: Despite its exceptional strength, polycarbonate is lightweight, making it a preferred choice in applications where weight reduction is essential. Its versatility allows it to be easily molded into complex shapes and designs.
Heat Resistance: Polycarbonate exhibits good heat resistance, enabling it to withstand high temperatures without significant deformation or degradation. This property makes it suitable for applications where exposure to heat or thermal stress is anticipated.
Electrical Insulation Properties: Polycarbonate possesses excellent electrical insulation properties, making it valuable in applications where electrical components need to be protected from current leakage or short circuits.
Chemical Resistance: Polycarbonate demonstrates resistance to many chemicals, including oils, greases, and some acids. This property adds to its durability and suitability for various environments.
In conclusion, polycarbonate is a versatile thermoplastic polymer with a range of advantageous properties. Its manufacturing process and inherent characteristics make it a valuable material for a wide array of applications in industries such as automotive, electronics, construction, and consumer goods.
2. Applications of Polycarbonate
Polycarbonate's unique combination of properties makes it highly suitable for a wide range of applications across various industries. Here are some notable applications of polycarbonate:
2.1 Automotive Industry
2.1.1 Windows and Windshields:
Polycarbonate is extensively used in the automotive industry for the manufacturing of windows and windshields. Its high impact resistance helps ensure passenger safety by providing protection against rocks, debris, and collisions. Polycarbonate windows and windshields also offer excellent optical clarity and UV protection.
2.1.2 Exterior Components:
Polycarbonate is utilized in the production of exterior components for automobiles. This includes parts such as bumpers, grilles, body panels, and mirror housings. The material's impact resistance, lightweight nature, and design flexibility make it an ideal choice for enhancing vehicle aesthetics and durability.
2.2 Electronics Industry
2.2.1 Electronic Device Casings:
Polycarbonate is commonly used for electronic device casings, such as mobile phones, laptops, tablets, and gaming consoles. Its ability to withstand impact, scratch resistance, and design versatility make it an excellent choice for protecting electronic components while providing an attractive and ergonomic design.
2.2.2 Display Screens:
Polycarbonate plays a crucial role in the production of display screens. It is used as a protective layer or cover for screens in smartphones, tablets, televisions, and monitors. Polycarbonate provides high impact resistance, optical clarity, and scratch resistance, ensuring durability and optimal viewing experience.
2.3 Construction and Architecture
2.3.1 Skylights and Roofing:
Polycarbonate is widely employed in skylights and roofing systems due to its exceptional light transmission properties and impact resistance. It allows natural light to enter buildings, reducing the need for artificial lighting while offering durability and resistance to weather conditions.
2.3.2 Safety Glazing:
Polycarbonate is used for safety glazing applications in construction and architecture. It is commonly used for windows, doors, and partitions in areas that require enhanced impact resistance, such as sports facilities, schools, and high-risk environments. Polycarbonate's ability to withstand impacts without shattering improves safety and security.
2.4 Consumer Goods and Packaging
2.4.1 Bottles and Containers:
Polycarbonate is utilized in the production of bottles and containers for various industries, including water bottles, food storage containers, and baby bottles. Its durability, lightweight nature, and resistance to impacts and chemicals make it a preferred material for packaging applications.
2.4.2 Household Items:
Polycarbonate is used in the manufacturing of various household items. This includes kitchenware such as food storage containers, utensils, and microwave-safe dishes. Additionally, it finds applications in lighting fixtures, decorative items, and even furniture due to its impact resistance, design flexibility, and transparency.
These are just a few examples of the wide range of applications where polycarbonate demonstrates its versatility and reliability. Its unique properties continue to drive its use in industries that require strength, durability, transparency, and safety.
3. Advantages of Polycarbonate
Polycarbonate offers numerous advantages that make it a preferred choice in various industries. Here are some key advantages of polycarbonate:
3.1 High Impact Resistance
Polycarbonate is renowned for its exceptional impact resistance, making it significantly more durable than many other plastics. It can withstand intense impacts without breaking or shattering, making it suitable for applications that require robust and reliable materials. This property is particularly important in industries such as automotive, construction, and electronics, where protection against impact is crucial for safety and longevity.
3.2 Transparency and Optical Clarity
Polycarbonate exhibits high transparency and optical clarity similar to glass. It allows for excellent light transmission, making it an ideal material for applications that require visibility or transparency. This advantage is particularly valuable in industries such as automotive, electronics, and architecture, where clear vision, display screens, or natural light transmission are desired.
3.3 Lightweight and Versatile
Despite its exceptional strength and impact resistance, polycarbonate is remarkably lightweight compared to other materials such as glass. This lightweight property makes it easier to handle and transport, reduces energy consumption in transportation, and allows for more design flexibility. Polycarbonate's versatility further extends to its ability to be easily molded into complex shapes and forms, opening up possibilities for innovative designs and customized applications.
3.4 Heat Resistance
Polycarbonate exhibits good heat resistance, enabling it to withstand high temperatures without significant deformation or degradation. It can withstand both low and high-temperature extremes, making it suitable for applications that involve exposure to heat, such as automotive components, electronic enclosures, lighting fixtures, and construction materials. Its heat resistance ensures the material's stability and integrity, even in demanding environments.
3.5 Electrical Insulation
Polycarbonate possesses excellent electrical insulation properties. It acts as an effective insulator, preventing the flow of electric current and minimizing the risk of electrical hazards such as short circuits or electrical leakage. This property makes polycarbonate an ideal material for electrical and electronic applications, including circuit boards, electrical enclosures, connectors, and insulating components. Its electrical insulation properties contribute to the safety and reliability of electrical systems and devices.
In conclusion, polycarbonate offers several advantages that contribute to its widespread use in numerous industries. Its high impact resistance, transparency, lightweight nature, heat resistance, and electrical insulation properties make it a versatile and reliable material. Whether it's for safety, aesthetics, durability, or functional requirements, polycarbonate's advantageous properties continue to drive its popularity in a wide range of applications.
4. Manufacturing and Processing of Polycarbonate
Polycarbonate is manufactured through a series of processes involving monomer synthesis and polymerization. Once the polymer is produced, it can undergo various processing techniques to shape it into desired forms. Here are the key steps involved in the manufacturing and processing of polycarbonate:
4.1 Monomer Synthesis
The first step in polycarbonate production is the synthesis of the monomer bisphenol A (BPA). BPA is synthesized through a reaction between phenol and acetone. The reaction typically takes place in the presence of an acid catalyst, resulting in the formation of BPA as the primary monomer for polycarbonate production. The quality and purity of the synthesized BPA are critical for achieving high-quality polycarbonate.
4.2 Polymerization
Once the BPA monomer is obtained, it undergoes polymerization to form the polycarbonate polymer. The polymerization process involves combining the BPA monomer with phosgene gas (COCl2). This reaction results in the formation of polycarbonate chains through the linkage of carbonate groups between the BPA molecules.
The polymerization process can be controlled to achieve the desired molecular weight and properties of the polycarbonate. Different catalysts, reaction conditions, and additives can be used to tailor the characteristics of the final polymer, such as its transparency, impact resistance, and thermal stability.
4.3 Injection Molding
Injection molding is a widely used technique for shaping polycarbonate into various forms, including complex shapes and intricate details. In this process, the polycarbonate is heated to a molten state and then injected into a mold under high pressure. The molten polycarbonate fills the mold cavity and solidifies, taking the shape of the mold.
Injection molding offers several advantages, including high production efficiency, precise control over part dimensions, and the ability to produce large quantities of parts with consistent quality. It is commonly used in the production of automotive components, electronic enclosures, consumer goods, and other applications where intricate shapes and high volumes are required.
4.4 Extrusion
Extrusion is another commonly employed method for processing polycarbonate. It involves heating the polycarbonate resin to a molten state and forcing it through a specially designed die to form continuous profiles, sheets, or other linear forms. The extruded polycarbonate is then cooled and solidified to obtain the desired shape.
Extrusion is versatile and allows for the production of long, continuous sections of polycarbonate with consistent dimensions. It is often used for applications such as profiles for construction, glazing systems, tubing, and pipes.
4.5 Thermoforming
Thermoforming is a process that involves heating a polycarbonate sheet to a pliable temperature and then forming it into a specific shape using a mold or vacuum. The heated sheet is placed over the mold, and either vacuum pressure or mechanical force is applied to draw the polycarbonate onto the mold surface, creating the desired shape. The formed polycarbonate is then cooled and trimmed to the final dimensions.
Thermoforming is commonly used for applications such as packaging, signage, automotive interior parts, and consumer goods. It offers cost-effectiveness, rapid production, and the ability to create complex shapes with good surface finish.
In conclusion, the manufacturing and processing of polycarbonate involve the synthesis of the monomer bisphenol A, followed by polymerization to form the polycarbonate polymer. Once the polymer is obtained, it can be processed using techniques such as injection molding, extrusion, and thermoforming to shape it into various forms for different applications. These processes enable the production of high-quality polycarbonate parts and products with desired properties and dimensions.
5. Comparison with Other Plastics
Polycarbonate is a versatile thermoplastic that has unique properties and advantages compared to other plastics. Here, we compare polycarbonate with three commonly used plastics: acrylic, PET (polyethylene terephthalate), and ABS (acrylonitrile butadiene styrene).
5.1 Polycarbonate vs. Acrylic
Polycarbonate and acrylic (also known as PMMA, or polymethyl methacrylate) are both transparent plastics frequently used in similar applications. However, they differ in several aspects:
Impact Resistance: Polycarbonate is significantly more impact-resistant than acrylic. Polycarbonate can withstand intense impacts without breaking, making it suitable for applications requiring high durability and safety, such as automotive windows. Acrylic, on the other hand, is more prone to cracking or shattering upon impact.
Clarity: Acrylic generally offers better optical clarity and transparency than polycarbonate. Acrylic provides exceptional light transmission, making it preferred for applications where optical clarity is paramount, such as display cases or signage.
Chemical Resistance: Polycarbonate exhibits better resistance to chemicals compared to acrylic. Polycarbonate is less susceptible to damage from common household chemicals, oils, and greases.
Cost: Acrylic is generally more cost-effective than polycarbonate. Acrylic offers a balance between cost and optical clarity, making it a popular choice for various applications where impact resistance is not the primary concern.
5.2 Polycarbonate vs. PET
Polycarbonate and PET are both thermoplastics commonly used in packaging and other applications. Here are some key differences:
Strength and Impact Resistance: Polycarbonate is significantly stronger and more impact-resistant than PET. Polycarbonate's high impact resistance makes it suitable for applications requiring durability and protection against impact, such as safety goggles or electronic device casings. PET, while strong, is more prone to cracking or breaking under heavy impact.
Clarity: Both polycarbonate and PET offer good clarity, but polycarbonate has slightly better optical properties, providing higher light transmission. This makes polycarbonate more suitable for applications where optical clarity is essential.
Temperature Resistance: Polycarbonate has better heat resistance than PET. Polycarbonate can withstand higher temperatures without significant deformation or degradation. PET has a lower heat resistance, limiting its suitability for applications involving high temperatures.
Chemical Resistance: Polycarbonate has better chemical resistance compared to PET. It is more resistant to chemicals, oils, and greases, making it suitable for applications where contact with these substances is expected.
5.3 Polycarbonate vs. ABS
Polycarbonate and ABS are two popular thermoplastics used in various industries. Here are some key differences between them:
Impact Resistance: Polycarbonate has superior impact resistance compared to ABS. Polycarbonate can withstand heavy impacts without breaking, while ABS is more prone to cracking or deformation.
Heat Resistance: Polycarbonate exhibits better heat resistance than ABS. Polycarbonate can tolerate higher temperatures without significant deformation or loss of properties. ABS has a lower heat resistance and can soften or warp at higher temperatures.
Chemical Resistance: ABS generally offers better chemical resistance than polycarbonate. ABS is more resistant to a wider range of chemicals, including acids and bases, while polycarbonate is susceptible to certain chemicals.
Processing: ABS is easier to process and has better flow characteristics during injection molding compared to polycarbonate. ABS is often preferred for applications that require intricate shapes and details.
Applications: Polycarbonate is commonly used in applications where high impact resistance and optical clarity are required, such as automotive components, safety equipment, and electronic devices. ABS is frequently used in applications such as automotive interiors, consumer goods, and toys, where a balance of impact resistance, processability, and cost is essential.
6. Environmental Considerations
Polycarbonate, like other plastics, has environmental considerations associated with its production, use, and disposal. Here are some key points regarding the environmental aspects of polycarbonate:
6.1 Recycling and Sustainability
Recycling: Polycarbonate is recyclable, and recycling initiatives can help reduce its environmental impact. However, recycling polycarbonate can be challenging due to its high molecular weight and the need for specialized recycling processes. Mechanical recycling is commonly used, where polycarbonate waste is melted and reprocessed into new products. Chemical recycling methods are also being explored to break down polycarbonate into its monomer form for reuse. Proper collection, sorting, and recycling infrastructure are crucial to promote the recycling of polycarbonate products.
Sustainability: Polycarbonate is derived from non-renewable fossil fuels, and its production requires energy and natural resources. However, efforts are being made to improve the sustainability of polycarbonate. Some manufacturers are incorporating bio-based or recycled content into polycarbonate production to reduce reliance on virgin fossil fuels. Additionally, advancements in energy-efficient manufacturing processes and the use of renewable energy sources help minimize the environmental impact of polycarbonate production.
Life Cycle Assessment (LCA): Life Cycle Assessment is a comprehensive approach used to evaluate the environmental impact of a product throughout its life cycle, including raw material extraction, production, use, and end-of-life disposal. LCA studies provide insights into the environmental footprint of polycarbonate and guide efforts to reduce its impact by optimizing processes, increasing recycling rates, and promoting sustainable practices.
6.2 Environmental Impact
Energy Consumption: The production of polycarbonate requires energy, primarily derived from fossil fuels. Energy-intensive processes, such as monomer synthesis and polymerization, contribute to the overall environmental footprint of polycarbonate. The industry is working towards reducing energy consumption through process optimization and the use of renewable energy sources.
Greenhouse Gas Emissions: Polycarbonate production and its associated energy consumption contribute to greenhouse gas emissions, including carbon dioxide (CO2). Efforts are being made to reduce emissions by adopting cleaner technologies, improving energy efficiency, and utilizing renewable energy.
Waste and Disposal: Polycarbonate waste that is not recycled can end up in landfills or incineration facilities. Landfilling polycarbonate can contribute to the accumulation of plastic waste and its associated environmental concerns. Incineration may release greenhouse gases and other pollutants. Proper waste management practices, including recycling, are essential to minimize the environmental impact of polycarbonate disposal.
Environmental Regulations: Governments and regulatory bodies around the world are implementing regulations and standards to address the environmental impact of plastics, including polycarbonate. These regulations aim to promote recycling, reduce emissions, and encourage the use of sustainable materials. Compliance with these regulations ensures that polycarbonate manufacturers and users follow environmentally responsible practices.
Overall, while polycarbonate has its environmental considerations, efforts are underway to improve its sustainability and reduce its environmental impact. Recycling, promoting circular economy practices, reducing energy consumption, and adopting cleaner production technologies are crucial for minimizing the environmental footprint of polycarbonate and ensuring its responsible use.
7. Safety and Handling Precautions
When working with polycarbonate, it is important to follow appropriate safety guidelines and precautions to ensure the well-being of individuals and prevent potential hazards. Here are some key considerations related to the safety and handling of polycarbonate:
7.1 Health and Safety Guidelines
Personal Protective Equipment (PPE): When handling polycarbonate, it is recommended to wear appropriate personal protective equipment, including safety glasses or goggles, gloves, and protective clothing. PPE helps protect against potential eye or skin contact with molten polycarbonate, dust, or chemical additives.
Ventilation: Ensure proper ventilation in the working area when processing polycarbonate. Adequate ventilation helps to remove any fumes or gases released during the heating or processing of the material. This is especially important when using high temperatures or in enclosed spaces.
Dust Control: When cutting, grinding, or sanding polycarbonate, dust may be generated. Take necessary precautions to minimize dust exposure, such as using dust collection systems, wearing respiratory protection if required, and ensuring the work area is properly ventilated.
Safe Handling: Handle polycarbonate with care to prevent injury. Avoid sharp or rough handling that may cause scratches or cracks in the material. Protect polycarbonate sheets or parts from impacts or excessive force to maintain their integrity and prevent potential breakage.
7.2 Fire Safety
Fire Retardancy: Polycarbonate itself is not inherently fire-resistant. It is a flammable material and can melt, burn, or release toxic gases when exposed to high temperatures or flames. However, flame-retardant additives can be incorporated during the manufacturing process to enhance its fire resistance. When fire retardant properties are required, look for specific grades of polycarbonate designed for improved fire safety.
Fire Prevention: Take necessary precautions to prevent fires when working with or storing polycarbonate. Keep polycarbonate away from open flames, sparks, or other sources of ignition. Store polycarbonate materials in designated areas away from heat sources and combustible materials.
Firefighting Measures: In the event of a fire involving polycarbonate, use appropriate firefighting methods. Water spray, foam, or dry chemical extinguishers may be effective in controlling the fire. Follow local fire regulations and procedures, and ensure the safety of individuals nearby.
Safety Data Sheets (SDS): Refer to the Safety Data Sheets provided by the manufacturer for detailed information on safe handling, storage, and emergency procedures specific to the type of polycarbonate being used. SDS provides crucial information regarding potential hazards, first aid measures, and appropriate safety precautions.
It is essential to follow safety guidelines and take necessary precautions when working with polycarbonate to ensure the well-being of individuals and maintain a safe working environment. Adhering to health and safety guidelines, proper handling practices, and understanding fire safety measures contribute to the responsible use of polycarbonate and mitigate potential risks.
8. Future Trends and Innovations
Polycarbonate continues to evolve through ongoing research and development efforts, leading to new innovations and emerging applications. Here are some future trends and potential advancements in the field of polycarbonate:
8.1 Research and Development
Enhanced Properties: Researchers are continually exploring ways to improve the properties of polycarbonate. This includes efforts to enhance its impact resistance, optical clarity, heat resistance, and chemical resistance. Through material modifications and the incorporation of additives or reinforcements, advancements in polycarbonate formulations aim to expand its range of applications.
Sustainable Manufacturing: The focus on sustainability and environmental impact is driving research into more sustainable manufacturing processes for polycarbonate. This includes investigating alternative feedstocks derived from renewable resources and exploring energy-efficient production methods. Additionally, the development of more efficient recycling techniques and the utilization of recycled polycarbonate as a raw material are key areas of research.
Advanced Processing Techniques: Advances in processing techniques, such as additive manufacturing (3D printing), are being explored to expand the possibilities of polycarbonate. Additive manufacturing allows for complex geometries and customized designs, opening up new avenues for the production of intricate polycarbonate components.
Nanotechnology and Composites: The integration of nanotechnology and composite materials into polycarbonate matrices is an area of active research. By incorporating nanoparticles or reinforcing fibers, researchers aim to enhance the mechanical, thermal, and electrical properties of polycarbonate. This may lead to the development of polycarbonate-based materials with improved strength, conductivity, or specific functionalities.
8.2 Emerging Applications
Automotive Glazing: The automotive industry is increasingly adopting polycarbonate for glazing applications, such as windows and windshields. Polycarbonate offers significant weight reduction compared to glass, contributing to improved fuel efficiency and reducing vehicle emissions. Advancements in coatings and surface treatments also address concerns related to scratch resistance and UV protection.
Flexible Electronics: Polycarbonate's transparency, flexibility, and excellent electrical insulation properties make it suitable for emerging applications in flexible electronics. Flexible displays, touch sensors, and wearable devices can benefit from the lightweight and versatile nature of polycarbonate, enabling new possibilities for the integration of electronics into flexible and curved surfaces.
Energy Storage: Polycarbonate's thermal and electrical insulation properties make it a promising material for energy storage applications. Polycarbonate-based separators for batteries and supercapacitors can offer improved safety, enhanced thermal stability, and efficient ion transport, contributing to the development of advanced energy storage technologies.
Smart Windows: Polycarbonate is being explored for the development of smart windows that can dynamically control light transmission and heat insulation. By incorporating smart coatings or embedded nanoparticles, polycarbonate windows can switch between transparent and opaque states or regulate the amount of infrared radiation transmitted, contributing to energy-efficient building designs.
As research and development efforts continue, polycarbonate is likely to find new applications and witness advancements in its properties and manufacturing processes. The future holds exciting possibilities for polycarbonate, contributing to its versatility and expanding its range of uses across various industries.
In conclusion, polycarbonate is a versatile and widely used thermoplastic that offers numerous advantages and applications. It is known for its high impact resistance, transparency, lightweight nature, heat resistance, and electrical insulation properties. Polycarbonate finds applications in various industries, including automotive, electronics, construction, and consumer goods. It is used for windows, windshields, electronic device casings, display screens, skylights, safety glazing, bottles, containers, and household items.
When compared to other plastics, polycarbonate stands out for its superior impact resistance, transparency, and heat resistance. However, it may have some limitations in terms of cost, optical clarity, and chemical resistance when compared to specific plastics like acrylic, PET, or ABS.
The manufacturing and processing of polycarbonate involve steps such as monomer synthesis, polymerization, injection molding, extrusion, and thermoforming. These processes contribute to the production of high-quality polycarbonate products with specific shapes and properties.
Considering environmental considerations, recycling and sustainability efforts are being made to minimize the environmental impact of polycarbonate. Proper recycling infrastructure and the use of recycled or bio-based content in production are steps taken towards a more sustainable approach. Life cycle assessment studies help evaluate and improve the environmental footprint of polycarbonate.
Safety and handling precautions are crucial when working with polycarbonate. Following health and safety guidelines, wearing appropriate personal protective equipment, ensuring proper ventilation, and considering fire safety measures are essential to prevent hazards and maintain a safe working environment.
Looking towards the future, ongoing research and development in polycarbonate focus on enhancing its properties, exploring sustainable manufacturing processes, advancing processing techniques, and investigating emerging applications. These advancements may lead to improved versions of polycarbonate, expanded applications in various industries, and the development of innovative products.
Overall, polycarbonate continues to be a valuable material with a wide range of applications and promising prospects for the future. Its unique properties, versatility, and ongoing innovations make it an important choice for various industries seeking high-performance and reliable materials.
Read more:
Raw Material of HDPE of Parsethylene Kish
High Density Polyethylene
Polyethylene Pipe | HDPE PIPES
Polyethylene Pipe (PE pipe)Polyethylene fittings
Polyethylene manhole