
Polyethylene pipe inspection checklists
QC of HDPE Pipe
Inspection of the polyethylene pipe has different checklists and depends on what institution undertakes the inspection. The quality control unit and laboratory located in the company monitor all production conditions according to their own responsibilities.
• Entrance, transportation and storage of raw materials at the factory
• Checking the quality of raw materials and recording the results in tractable forms and comparison with requirements and standards
• Polyethylene pipe production process
• The correct quality and function of machinery and production line
• Physical, apparent and dimensional control of the produced polyethylene pipe
• Storage of pipes at the factory site after production
• Conduction of compulsory tests on the final product according to the standard and recording the results in predefined and traceable forms.
• Finally, monitoring the transportation of pipes to the customer and the project site
Each of the above steps has certain standards according to which the steps shall be carried out and the best reference for understanding the methods and standards is the Polyethylene Pipe Handbook.
The most important tests performed on these pipes are:
• The weight percentage of soot or carbon in polyethylene
• Density determination
• Flexural, pressure and elasticity coefficient tests
• Pipe tolerance threshold tests against internal pressure
• Tests of pipes’ physical properties (Dimensions - Diameter - Color)
• Cyclic strength of pipe
• Oxidation of pipes (thermal stability)
• Polyethylene Viscosity
• Hydrostatic Testing

Inspections carried out by inspectors chosen by the customer and the contractor to check and ensure the quality of the polyethylene pipe, has 3 levels:
• Level A of polyethylene pipe inspection:
At this level of inspection, all steps mentioned above are carried out in the presence of the representative and the inspector, and the polyethylene materials are tested in the presence of the inspector and, after approval, enter the extruder and the production line, and the inspector is present until the end and carrying the polyethylene pipes. He personally confirms the results of the quality control tests.
• Level B of polyethylene pipe inspection:
At the second level of polyethylene pipe inspection, the raw material and production line are commissioned, and the inspector verifies the process in terms of appearance and checks the product in a randomized manner and compares the results with the standards, and the laborartory documents are as the basis for the remaining tests and processes.
• Level C of polyethylene pipe inspection:
At this level of inspection, which is the easiest inspection, the inspector is present at the factory site, examining the pipes produced in terms of appearance and dimensions, and relies on the documents and tests carried out by the factory's quality control for the remaining items.
It should be noted, however, that if the quality control laboratory has the required standards, an ISO 17025 certificate, accredited components, and committed personnel, all laboratory documents are reliable and valid, and the factory's quality control unit itself runs the toughest tests and the product is 100% high quality.
What is ITP?
Some projects have ITP, and the inspector performs inspections based on ITP, and the checklist is specified within ITP. ITP stands for: Inspection Test Plan.
The first inspection session will be held in the presence of the employer, the representative of the inspection company and the manufacturer's representative, and discussions will be held on ITP and its details and the checklists of the HDPE Pipe inspection, and ultimately, an agreement will be signed between the parties on how to carry out the tests and checklists.
ITP is extracted from the standard text that can be more difficult or easier than standard, which is usually stricter than standard.
And projects that do not have ITP, tests and checklist are carried out on the base of the standards.
White raw material tests for the production of polyethylene pipe include:
1. Density test
2. MFR test
3. Thermal Stability Test (OIT)
4. The amount of volatile substances
The self-colored materials’ test includes the above items, as well as the testing of soot weight and the distribution and dispersion of soot.
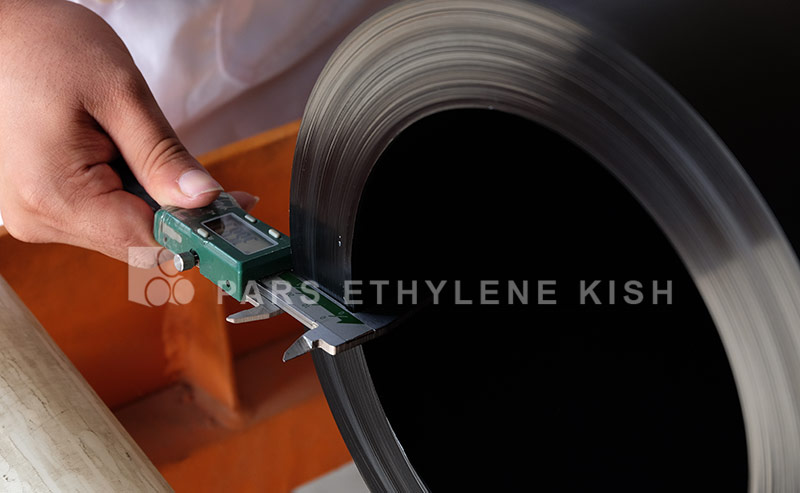
Single-wall water supply pipe tests include:
1. Soot weight percentage test
2. Soot distribution and dispersion test
3. Density test
4. Thermal Stability Test (OIT)
5. MFR Test
6. Thermal return test
7. Tensile test
8. Hydrostatic test 100 hours at 20 ° C
9. Hydrostatic test 165 hours at 80 ° C
Dimensional control including diameter, thickness, out-of-roundness and pipe appearance are controlled according to standard requirements.
Tests of two-wall pipes include:
1. Weight percentage of soot
2. Soot distribution and dispersion
3. Density
4. Thermal Stability (OIT)
5. Melt Flow Index (MFR)
6. Oven Test
7. Impact Test
8. Short-term cyclic rigidity test (3%)
9. Flexibility Test (30%)
10. Long-term cyclic rigidity test (SR24)
11. No leak test
Dimensional control is also performed on two-wall pipes.
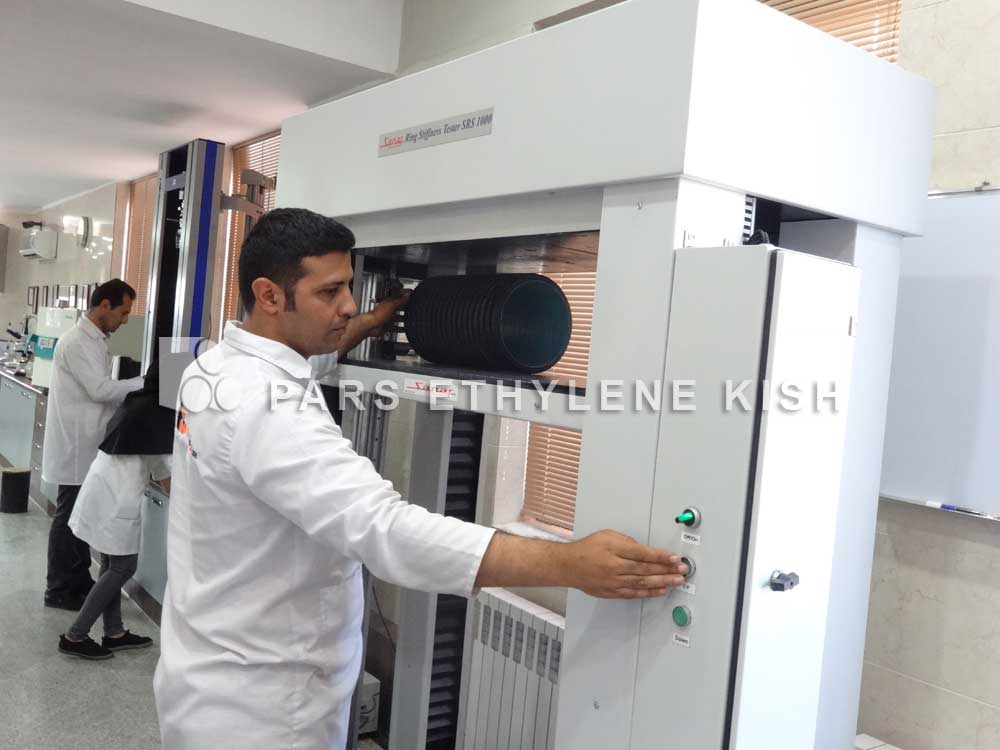
Checklist of Polyethylene Pipe Production Tests
The titles of polyethylene pipe production tests are as follows:
• Melt flow index ISO 1123
• Determining density ISO1183
• Determination of carbon content ASTM D 1603
• Tensile Test BS 2782 - EN63 - ASTM D 2412
• Hydrostatic pressure test EN 921
• Burst pressure test ASTM D 1599
• Thermal return test ISO 2505
• Measuring the dimensions and appearance of the pipe ISO11922
• O.I.T test
• Squeezing Test EN12106, ISO 4437
Melt Flow Index
In this test, the velocity of the melting material at a constant temperature and time is measured, in order to determine the results of the behavior of the materials inside the extruder.
This test is performed for raw material (for quality assurance) and also for the product. The product’s MFI value should not differ by more than 2% from the MFI of the raw material.
Density determination
Density of the raw materials and the product density is determined by flotation method using a precise and fluid scale with a specific density. Meanwhile, the product density value represents the quality of the production process.
Carbon content determination
The amount of carbon in the raw material and the final product is determined. For this purpose, a certain amount of the raw material in a furnace up to 800 ° C is subjected to pyrolysis of pure nitrogen gas and the amount of carbon remaining under the influence of oxygen is burned to determine the percentage of ash (additive) in the primary sample.
Permissible carbon content in the polyethylene pipe is 2 to 2.5% of weight percentage and should be uniformly distributed throughout it.
* In areas where carbon accumulation is more than permissible, tension will be concentrated and the pipes will be vulnerable, and if the carbon content is lower than the permissible limits, the pipe's resistance to ultraviolet rays of the sun will be reduced.
Pars Ethylene Kish Company believes that the use of the physical combination of soot and white granules reduces the quality of the manufactured pipe and therefore uses self-colored granules in their productions. For more information on this topic, please refer to the reason for using soot in polyethylene pipes.
Tensile test
Using the specialized laboratory devices, mechanical properties of polyethylene pipes, including maximum strength against external load, length variation at break point, determination of elasticity coefficient and scratches under the influence of three-point loads can be measured. Considering the results of this test, we can examine the performance of the product under operating conditions.
Hydrostatic pressure test
To test the strength of the product against hydrostatic pressures, the above test is performed. In this experiment, the pipe samples after immersion in the water basin, are placed under constant internal pressure according to the size of the pipe and the type of raw material at 20 ° C for 100 hours, or 80 ° C for 165 hours, or 80 ° C for 1000 hours.
The occurrence of any defect in the specimens (fracture, swelling, local swelling, leakage and hair cracks) means that the product is defective.
Burst pressure test
In this test, the pipes are floated in a basin with a constant temperature of 23 ° C and then subjected to an increase in internal pressure so that they swell and burst in 60 to 70 seconds.
The pipes produced with good materials and the correct process undergo a plastic deformation and swell, and then burst in the form of a beak tip, in this case the breakage is perpendicular to the longitudinal axis of the pipe.
A pipe that burst without swelling or longitudinal cracks is unusable.
Thermal return test
In this test, samples with a length of approximately 30 cm are placed inside an oven, with a hot air circulation of (110 + 2) ° C for one to three hours (depending on the thickness of the pipe wall) and after cooling the length of the pipe will be less than the initial state at normal temperature this behavior in the installed pipes can change the pipe's roundness. Therefore, with the above test, the length change limit (up to 3%) is checked in the laboratory.
Measurement of dimensions and appearance of the pipe
HDPE pipes should be free of any roughness (internal and external) and deep porosity. Partial cavity can be ignored provided that they do not reduce the thickness to less than the permissible limit.
* Determining the thickness of the pipe wall using calibration calipers in the cutting section and the ultrasonic thickness gauge along a pipe branch.
* The outer diameter of the pipe is measured using a graded metal strip (cycrometer) and measured along the length of a branch of the pipe, and its mean value is reported.
* According to the standard, the amount of deformation in the pipe section and losing the ovality is measured after the pipe is produced, the limit of these fluctuations is determined according to the outer diameter of the pipe. It needs to be explained that the form of polyethylene pipe is changed during transport and installation due to its flexible nature, which is solved after the connection operation and it entirely returns to its original form after implementation and movement of the fluid inside the pipe and applying pressure.
O.I.T. test
This test is performed on raw materials and the purpose of this test is to determine the thermal stability of the materials according to the standard, the time of destruction of polyethylene should not be less than 20 minutes.
Squeezing Test
In this test, samples with a size 8 times greater than the nominal diameter of the pipe are prepared and placed in zero-degree water for 10 hours. After squeezing of the pipe by squeezer machine for 1 hour, the pipe will return to its initial state through re-rounding machine. Then, with the closure of both ends of pipes with cope, the pipe is exposed to pressure of 8 bars for 1000 hours at 80 ° C temperature. According to the above standard, there should be no kind of crack in the pipe.
Quality Control Laboratory
17025 Certificates
Single wall polyethylene pipe laboratory
Corrugated Pipe Laboratory
Polyethylene pipe quality control
Polyethylene pipe inspection checklists
The Reason for High Quality of Pars Ethylene Kish Products
Reasons of paying attention to quality
Guaranty and after sales service
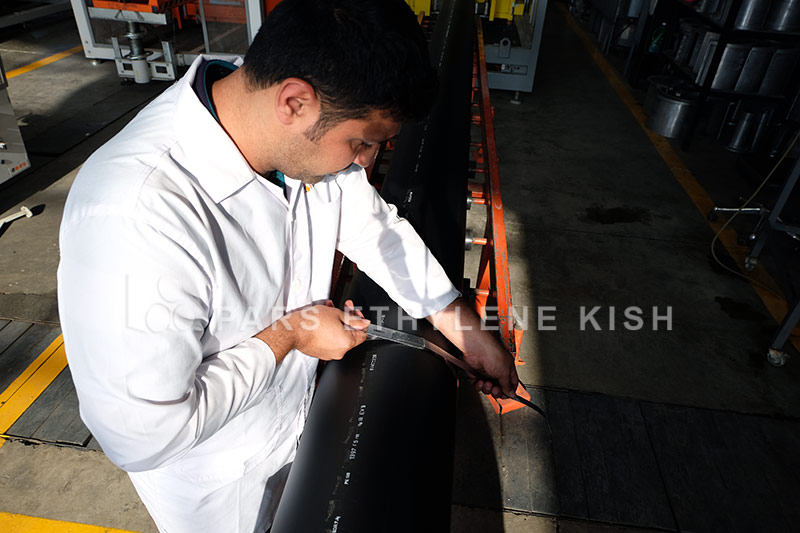
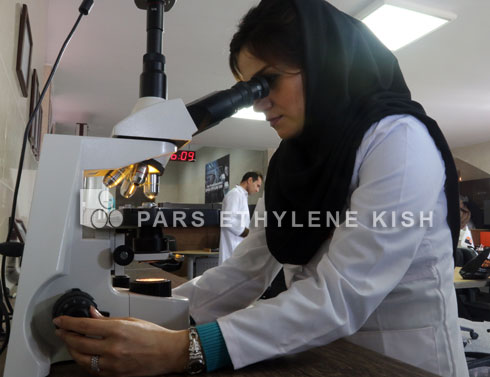
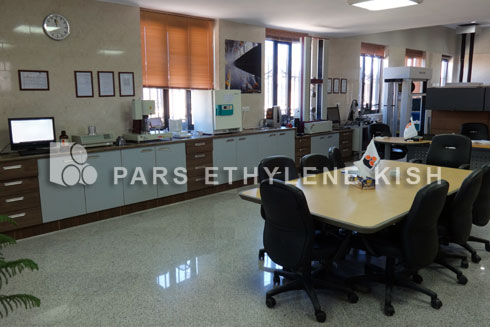
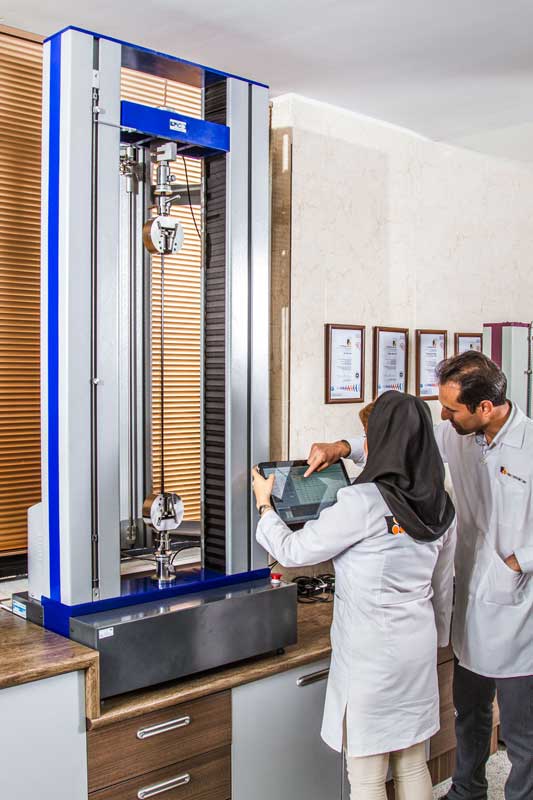
