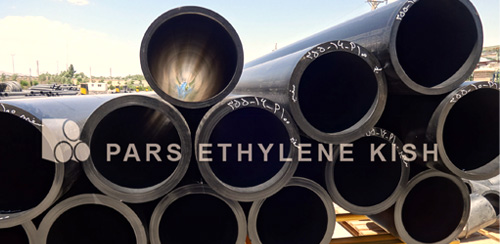
What is SDR ?
SDR in Polyethylene pipes
SDR stands for Standard Dimension Ratio. SDR is the ratio of the outer diameter to the thickness of the PE pipe, which is one of the characteristics of the Polyethylene pipe, and the pipes can be sorted according to the standard tables accordingly. The SDR value of Polyethylene Pipe is the main factor in determining the resistance of the pipe against the forces during installation and work pressure.
Definition of SDR with an example
For example, SDR11 means that the outer diameter of the PE pipe is 11 times of the wall thickness. As a result, the higher the SDR, the
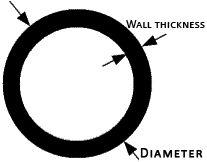
lower the pipe pressure will be. The details are discussed below.
For PE pipes, a dimensionless number is also defined, which is the ratio of the pipe diameter to the thickness of the pipe, which is referred to as the SDR. For example, for a 110 mm PE pipe with a pressure of 4 times made of PE80 materials, weighing 1.17 kg, it is SDR33, and for an PE pipe with a diameter of 110 mm made of PE80, weighting 1.77 kg, it is SDR21. Therefore, for a 110 mm diameter pipe, SDR decreases as the thickness increases due to the constant diameter (leading to increased pressure). SDRs range from 5 to 51, and the smaller the SDR is, the greater the pipe thickness and the lower pipe diameter will be.
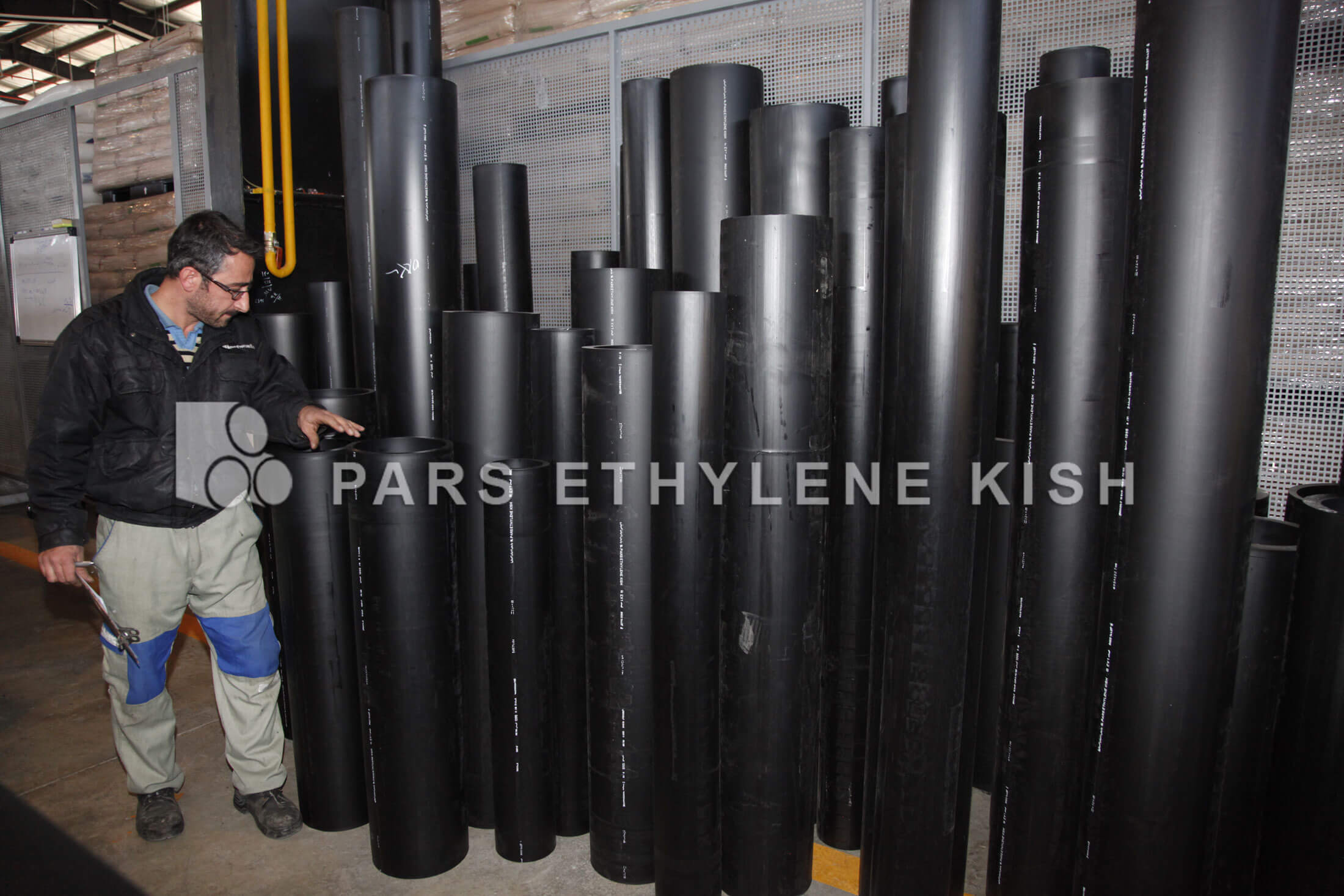
Types of PE pipes are manufactured at various working pressures and in SDRs or standard dimensions ratios including 33, 26, 22, 21, 17.6, 17, 13.6, 11, 9, 7.4, 6. Experience has shown that the use of PE pipes with SDR17 is suitable for gravity sewage applications and thinner pipes with SDR 19 to 21 are suitable for shorter and smaller diameter applications. Thin pipes severely deflect during installation and pipelining.
In the case of pressure applications, if the maximum permissible design pressure is less than 100 psi, the use of SDR17 is sufficient. If the maximum permissible design pressure exceeds 100 psi, the permissible value determines the SDR. If the permissible pressure value is equal to 150 psi, the PE pipes with SDR11 will have the pressure requirements. In most non-trench applications, and not in all of them, a pipe that can withstand the tensile stresses during installation will also be able to withstand vertical downward pressures and traffic pressures.
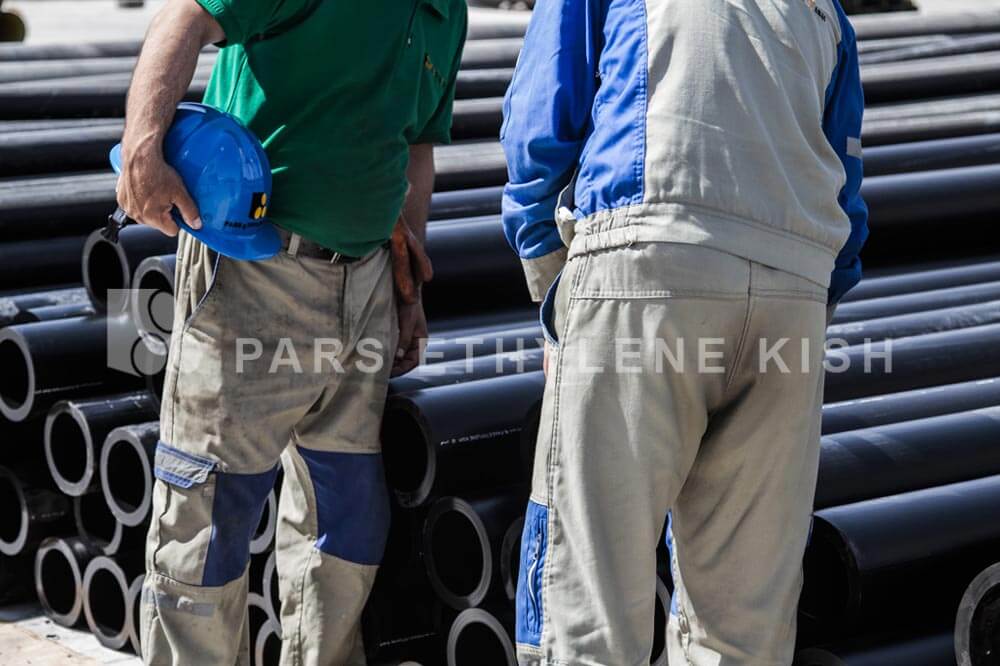

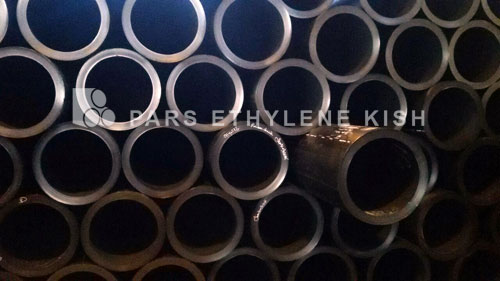
