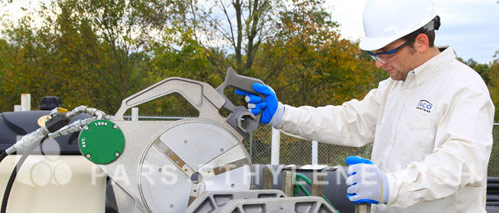
Polyethylene pipe welding and polyethylene fittings
Welding of polyethylene pipes
We will fully describe thewelding of Polyethylene pipe and fittings of Pars Ethylene Kish Company based on Butt Fusion method. We will also describe the welding process of polyethylene pipes, fittings and otherpolyethylene pipes with different dimensions and pressures through diagrams.
One of the most important points noticeable in the implementation of the polyethylene pipes network is the method of welding pipes and fittings. Pipes and fittings are welded in two ways: Electro Fusion and Butt Fusion. Of course, there are other methods that are less common and not very useful.
The Butt Fusion method is taught in this text. The butt fusion of polyethylene pipes of Pars-Ethylene-Kish Company is very simple and fast compared to the welding of metal pipes. For this reason, proper training and compliance with welding conditions are important.
Polyethylene pipe welding machine must be provided to a person who knows the method and instructions for using the appliance and, secondly, knows the conditions for the preparation of pipes and eye examinations, and thirdly, follows the instructions for doing the butt fusion according to the right order.
Polyethylene pipe welding instruction tries to provide important points regarding visual inspection of welding and welding’s physical characteristics. In addition, the full description of the operation of the welding machine is given and specific recommendations are provided for the operation and safety of the process.
It is recommended to read the standard version of the polyethylene pipe welding.

The main titles of the Polyethylene Pipe Welding Instruction:
-
Introduction
-
Butt fusion method
-
Butt fusion steps
-
Important recommendations in butt fusion
-
Operation of the welding machine
-
Safety in polyethylene pipes welding
-
Butt fusion tables
Important recommendations of Pars-Ethylene-Kish Company for butt fusion of polyethylene pipes
-
Pipes and fittings must necessarily be manufactured in a factory; otherwise, the location of welding and connection will be cracked and broken.
-
Only those pipes can be placed under this type of welding which are identical in terms of diameter and thickness, and secondly, are completely identical in terms of produced material.
-
Before welding, the surfaces of the iron must be thoroughly cleaned. For this purpose, it is necessary to make a Dummy Join before the main welding of the pipes.
-
Always check the correctness of the operation of the iron thermostat through exact digital thermometers to ensure that the needed temperature is supplied for the iron.
-
Except when the iron is placed between the two pipes, this device must always be stored in the appropriate pod to be protected from wind, dust and dirt.
-
It is always necessary to cover two welded pipes that are out of the device with special caps to prevent the rapid flow of air, otherwise they will quickly cool and become defective.
-
It is advisable to expand a clean and appropriate substrate underneath the welding device to that contamination and particles of the surrounding environment do not disturb the work.
Guideline for Correct Welding of Polyethylene Pipes and Fittings of Pars Ethylene Kish Company
Procedure of intended for PA-11 fuel gas pipe (per ASTM D 2513) that has a grade designation (in accordance with PPI TR-4) of PA 32312.
Guideline for Correct Welding of Polyethylene Pipes and Fittings of Pars Ethylene Kish Company
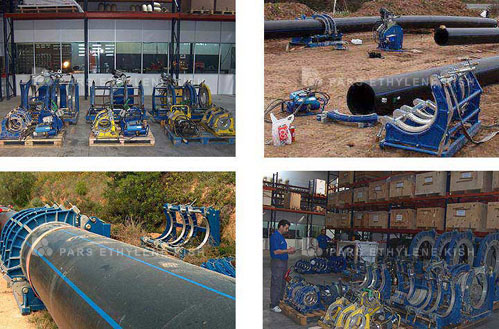
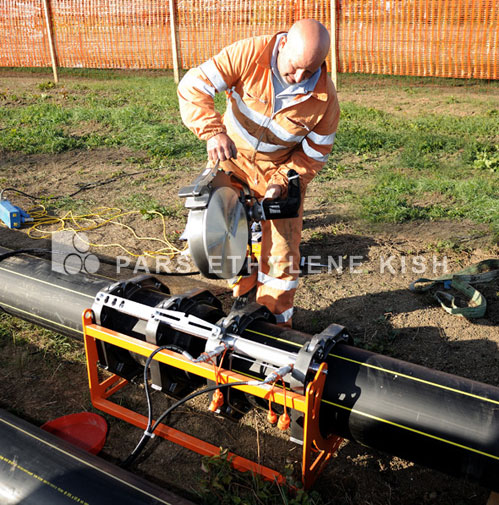
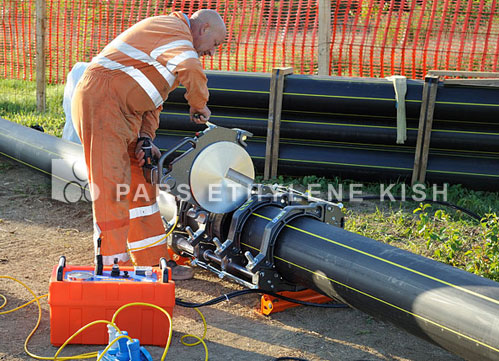
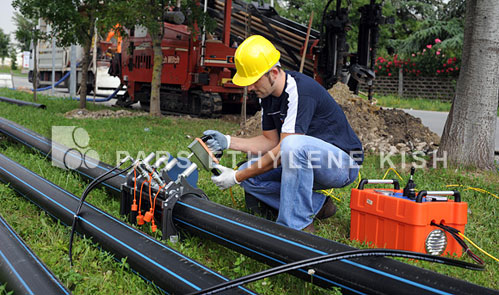