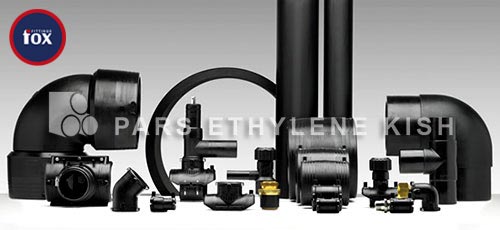
Polyethylene Electrofusion Fittings
Electrofusion joints For HDPE Pipelines
Electrofusion Fittings are a variety of fittings that can be used in gas pipelines and water supply lines. Electrofusion Fittings are a heat treatment method compared to butt fusion methods and electric is used to generate heat. Due to its high immunity, this method is the only type of connection approved for IGS standard for gas transmission lines. Using this method,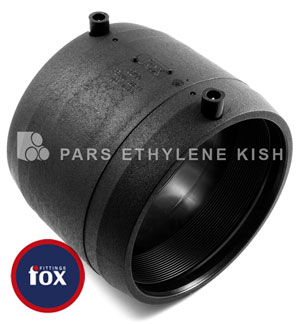
different polyethylene connections can be made, such as tube pipe, tube-knee, tube-bush (for example, in changing the diameter of the pipeline, etc.).
Therefore, there is no limitation of the polyethylene butt boiling method about tube connection of similar size. Also, the experience has shown that polyethylene connection can be connected to different types of polyethylene Along with its safety, the other advantages of this method are connection speed and cleanliness. But on the other hand, the limitation of this method at high cost and maximum diameter of the pipe can be connected with this method.
Pars Ethylene Kish is the exclusive and official representative of FOX Fittings of Europe in Iran and the Middle East. FOX Fittings is one of the leading manufacturers in the field of producing electrofusion joints in Europe and in the world. The company's electrofusion products and fittings are used worldwide through high quality. The FOX Fittings electrofusion fittings provided by Pars Ethylene Kish include coupler types, 90 ° and 45 ° knees, equal and unequal tees, converts, cups and saddles, and are manufactured at various sizes.
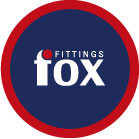
• Electrofusion Coupler SDR 11
• Electrofusion Coupler SDR 17
• Electrofusion Coupler SDR 9
• Electrofusion Coupler SDR 7.4
• SDR 11 Electrofusion Converter
• SDR 11 Electrofusion Splitter Belt
• SDR 11 Electrofusion Splitter
• SDR 11 Electrofusion Tee Belt
• SDR11 Electrofusion restoration belt
• TAPPING VALVE Belt
• Tee Electrofusion SDR 11
• Rectifier belt of HC Electrofusion SDR 11
• Tee Reducer SDR 11 electrofusion
• Tee BHZ Electrofusion SDR 11
• Electrofusion SDR 11 cap
• Elbow 90 BHZ Electrofusion Coupler SDR 11
• Elbow 90 Electrofusion SDR 11
• Elbow 45 Electrofusion BHZ Coupler SDR 11
• Elbow 45 ElectroFusion SDR 11
Electrofusion welding differs by the method of butt fusion welding. The main difference is in the heating method of the connection. In the fusion welding method, heaters are used to heat the pipe surface and the polyethylene joints, but in the electrofusion welding, the heat is generated internally and through the electric current. In polyethylene pipes, the electrofusion-induced welding strength is greater than head-to-head fusion welding. Electrofusion coupling is a common fitting for connecting two polyethylene tubes to each other.
Electrofusion welding is a type of pipe welding and polyethylene fittings, in which there are special connections that have electrical resistance wire to create welding melting temperatures. The electric current is transmitted through the electrofusion welding device and through the control box to the two ends of the connection. Like the thermal fusion welding (butt), a variety of saddle like and socket fittings are also used in the electrofusion method. The electrofusion boiling process is the same for most electrofusion joints.
Advantages of Electrofusion Fittings
• High safety and removal of obstacles and repairs
• Ease and quickly operate in runtime and save time
• High resistance to earthquakes and environmental stresses
• Flexibility and lightness
• Immune to corrosion
• Pressure and impact resistance
• Ease of installation, which prevents possible errors from the executives
• Eliminating gas and water waste in gas supply and water supply networks
• Smooth welding surface
• Ease of cleaning
• Avoid penetration into the welding area
• Avoid obstacles and damage
Electrofusion welding involves the following steps:
• Preparing the pipe for removing the gaps and cleaning the contaminants
• Marking the connection on the pipe, rubbing the pipe surface
• Reinforcing and applying strain on pipe or connector
• Applied electrical current
• Cooling, opening clips
• Documentation of the process
• Final payment, cleaning and removal of contaminants
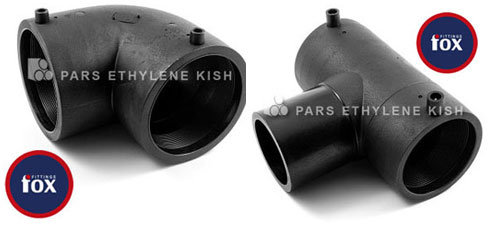
In the electric welding operation, it is necessary to observe the following points:
1- Heat distribution uniformly during boiling.
2. The temperature and pressure of the melted part must be carefully controlled.
3. Avoid damaging the coil of the coupler.
4- The necessary protection before, during and after the connection is necessary.
5- Consider the time to electrofusion.
6- The pipe is cut perpendicular to its axis and the roughness is cleaned with a flat sheath and a tube duct.
7- Clean any dirt from the pipe.
8- Make a connection piece in place and check for cleanliness.
9 - Shaved parts of the pipe should be cleaned with suitable materials. (Such as isopropanol)
10- For each connection of this type, the use of the clamp is necessary to maintain the connection set.
11- Due to the characteristics required in terms of voltage and welding time, necessary controls are required.
12 - The connection system inside the clamp remains until fully seamless.
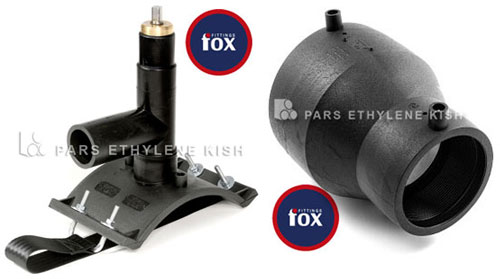
Connection of two Pipes using electrofusion joints
In this type of connection (electrofusion welding), a variety of connectors (electrofusion coupler) is used. The couplers are, in fact, polyethylene pieces in the form of a pipe or connection, in which the thermal element is located and the two ends of the element are connected to the power supply. First, the coupler includes a pair of tubes or joints that are supposed to be connected to each other. Then the two heads of the coupler are connected to the current and the plastic melts it. The created heat melts both ends of the connection and eventually the coupler covers the two ends of the head. After cooling down, the coupler metal clips are removed from the pieces.
We suggest visit HDPE Fitting Catalogue page

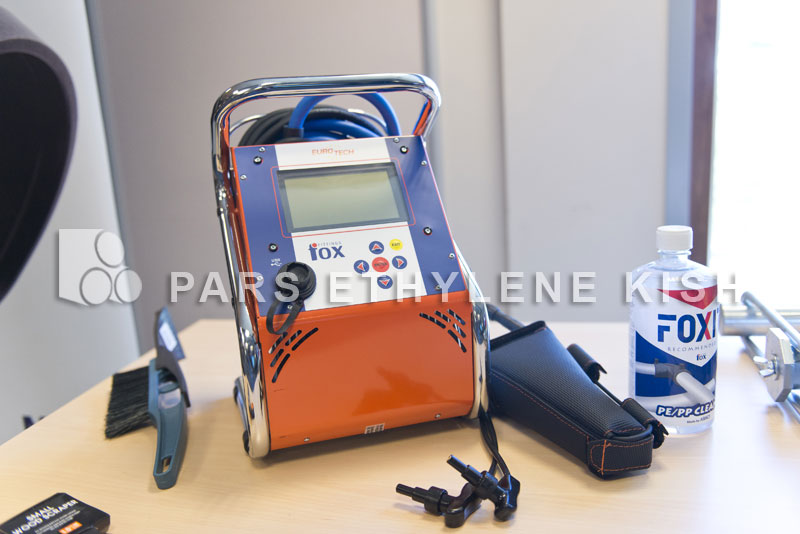
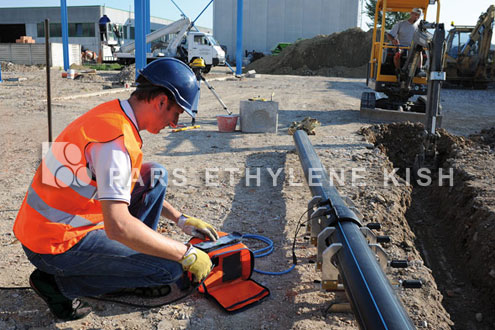
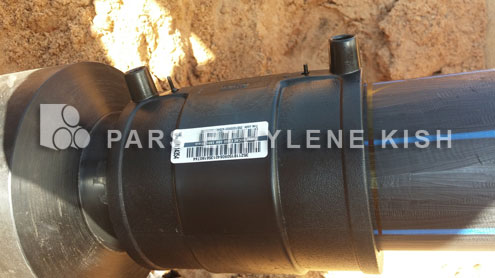
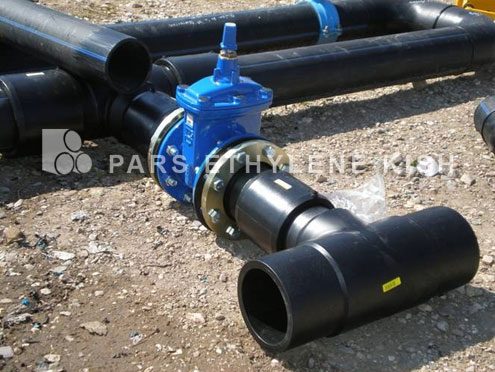
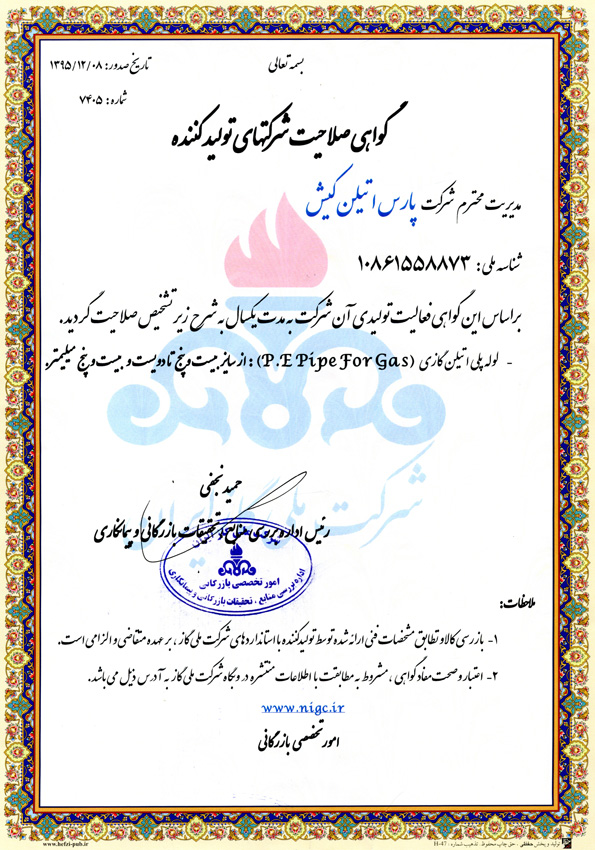