HDPE tubing
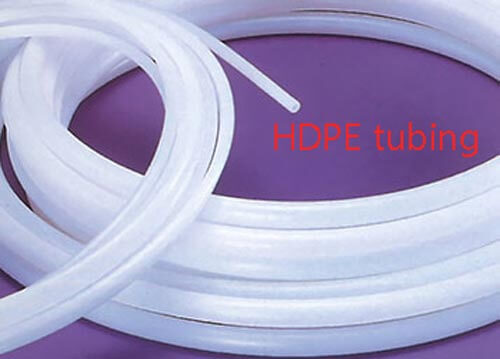
Introduction
HDPE tubing, or high-density polyethylene tubing, is a type of plastic tubing that is commonly used in a wide range of industrial and commercial applications. HDPE is a thermoplastic polymer that is made from petroleum-based hydrocarbons, and it is characterized by its high strength-to-density ratio, low coefficient of friction, excellent chemical resistance, and good impact resistance.
HDPE tubing is made through a process called extrusion, where raw HDPE material is melted and forced through a die to create a continuous tube shape. The tube can then be cut to the desired length and diameter for specific applications. HDPE tubing is available in various sizes, from small diameters used for medical tubing to large diameters used for water and gas pipelines.
HDPE tubing has several advantages over other types of tubing materials, including its high strength, resistance to chemicals and UV radiation, and flexibility. It is also relatively lightweight and easy to install, making it a cost-effective solution for many applications.
In addition to its strength and durability, HDPE tubing is also known for its resistance to a wide range of chemicals, including acids, bases, and solvents. This makes it an ideal choice for many chemical processing applications, such as those found in the pharmaceutical, food and beverage, and petrochemical industries.
Overall, HDPE tubing is a versatile and durable option for a wide range of industrial and commercial applications, thanks to its excellent combination of strength, flexibility, and chemical resistance.
Advantages of HDPE Tubing
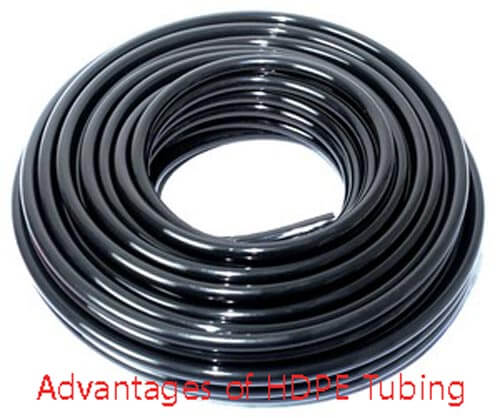
HDPE tubing, or high-density polyethylene tubing, offers several advantages over other types of tubing materials, making it a popular choice for a wide range of industrial and commercial applications. Here are some of the main advantages of HDPE tubing:
- High strength-to-density ratio: HDPE tubing is lightweight and has a high strength-to-density ratio, which means it is strong and durable while also being easy to handle and install. This makes it a cost-effective option for many applications.
- Chemical resistance: HDPE tubing is highly resistant to chemicals, including acids, bases, and solvents. This makes it an ideal choice for many chemical processing applications, such as those found in the pharmaceutical, food and beverage, and petrochemical industries.
- 3. UV resistance: HDPE tubing is also highly resistant to UV radiation, which means it can be used in outdoor applications without degradation or damage from exposure to sunlight.
- Flexible: HDPE tubing is flexible and can be easily bent and shaped to fit a wide range of applications. This flexibility also makes it easier to install in tight spaces and around corners.
- Corrosion-resistant: HDPE tubing is highly resistant to corrosion, which means it can be used in applications where other materials would quickly deteriorate and fail.
- Easy to weld and join: HDPE tubing can be easily welded and joined using a variety of techniques, including butt fusion, socket fusion, and electrofusion. This makes it easier to create custom lengths and shapes for specific applications.
Overall, the advantages of HDPE tubing make it a popular choice for a wide range of applications, including water and gas distribution systems, chemical processing, and industrial piping.
Polymer Properties
Polymers are large molecules made up of repeating units called monomers. They can be natural or synthetic, and they have a wide range of properties depending on their chemical composition and molecular structure. Here are some of the key properties of polymers:
- Strength and toughness: Polymers can have high strength and toughness, which makes them useful in applications where strength and durability are important.
- Flexibility: Many polymers are flexible and can be easily shaped or molded into different forms. This property makes them useful in applications where flexibility is important, such as in packaging materials.
- Chemical resistance: Polymers can be resistant to a wide range of chemicals, including acids, bases, and solvents. This makes them useful in applications where they will be exposed to harsh chemicals, such as in chemical processing and industrial applications.
- Thermal stability: Polymers can have high thermal stability, which means they can withstand high temperatures without degrading. This property makes them useful in applications where high temperatures are present, such as in aerospace and automotive industries.
- Electrical properties: Polymers can have a wide range of electrical properties, including conductivity, insulation, and dielectric strength. This makes them useful in applications where electrical properties are important, such as in electronics and telecommunications.
- Optical properties: Polymers can have a wide range of optical properties, including transparency, color, and refractive index. This makes them useful in applications where optical properties are important, such as in lenses and optical fibers.
Overall, the properties of polymers can be customized and tailored to specific applications, making them versatile and useful in a wide range of industries and applications.
Manufacturing Process
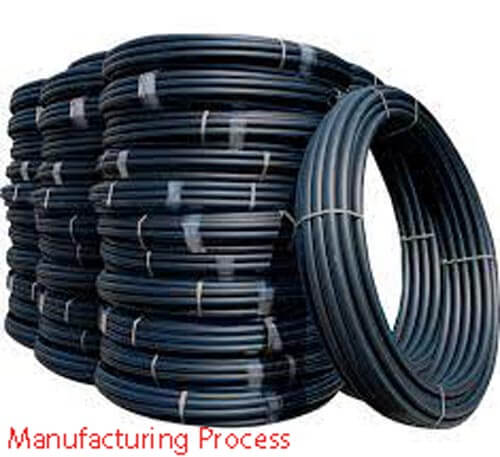
The manufacturing process for polymers can vary depending on the specific type of polymer being produced, but there are some general steps that are common to many polymer manufacturing processes. Here is an overview of the basic steps involved in the manufacturing of polymers:
- Monomer production: The first step in polymer manufacturing is to produce the monomers, which are the building blocks of the polymer. Monomers can be produced from natural sources or synthesized chemically.
- Polymerization: The next step is to polymerize the monomers into a polymer. Polymerization can be accomplished through a variety of methods, including chain-growth polymerization, step-growth polymerization, and emulsion polymerization.
- Purification: Once the polymer has been formed, it is often purified to remove any impurities and unwanted byproducts. This can be done through a variety of methods, including filtration and distillation.
- Processing: After purification, the polymer is ready for processing into a finished product. This can involve melting and molding the polymer into a specific shape, extruding it into a continuous length of tubing or sheeting, or other methods depending on the specific application.
- Finishing: Once the polymer has been processed into the desired form, it may undergo additional finishing steps, such as surface treatments or coatings, to enhance its performance or appearance.
Overall, the manufacturing process for polymers can be complex and may involve multiple steps and specialized equipment. However, advances in polymer science and technology have made it possible to produce a wide range of high-quality polymers for use in a variety of applications.
Types of HDPE Tubing
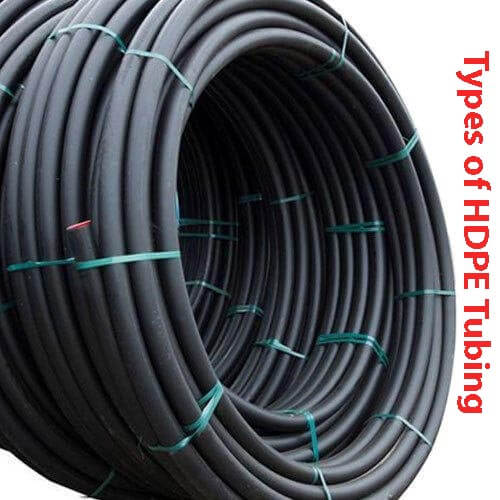
HDPE tubing, or high-density polyethylene tubing, comes in various types, each with different properties and uses. Here are some of the most common types of HDPE tubing:
- Standard HDPE tubing: This is the most common type of HDPE tubing and is often used in water and gas distribution systems, as well as in agricultural and industrial applications. It is known for its high strength, durability, and chemical resistance.
- Ultra-high molecular weight (UHMW) HDPE tubing: This type of HDPE tubing has an extremely high molecular weight, which makes it exceptionally resistant to abrasion and impact. It is commonly used in industrial applications, such as conveyor systems and chute linings.
- Flexible HDPE tubing: This type of HDPE tubing is more flexible and has a lower stiffness than standard HDPE tubing. It is often used in applications where flexibility is important, such as in medical devices, automotive fuel systems, and irrigation systems.
- Corrugated HDPE tubing: This type of HDPE tubing has a corrugated exterior that provides additional strength and flexibility, making it ideal for use in underground drainage systems, culverts, and other applications where strength and durability are important.
- Coiled HDPE tubing: This type of HDPE tubing comes in large coils and is commonly used in irrigation and sprinkler systems, as well as in residential plumbing systems.
Overall, the type of HDPE tubing used depends on the specific application and the required properties, such as strength, flexibility, and chemical resistance. HDPE tubing is a versatile material with many uses and applications, and the availability of different types of HDPE tubing allows for customization to meet specific needs.
Advancements in HDPE Tubing
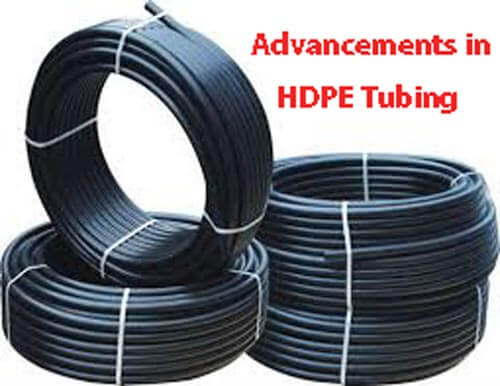
Advancements in HDPE tubing technology have led to improvements in the material's strength, durability, flexibility, and other properties, as well as expanded its range of applications. Here are some of the recent advancements in HDPE tubing:
- Improved manufacturing processes: Advances in polymer science and technology have led to improved manufacturing processes for HDPE tubing, resulting in better consistency and higher quality of the material.
- Enhanced resistance to chemicals: HDPE tubing has traditionally been known for its chemical resistance, but recent advancements in the material have led to even greater resistance to a wider range of chemicals, making it suitable for use in more demanding industrial and chemical applications.
- Increased strength and durability: Recent advancements in HDPE tubing technology have resulted in improved strength and durability, allowing it to withstand greater stresses and pressures. This has expanded the range of applications for HDPE tubing in industries such as oil and gas, mining, and construction.
- Better flexibility and ease of installation: Advances in HDPE tubing technology have also led to the development of more flexible and easier to install tubing, making it easier and more cost-effective to install in a wide range of applications.
- Improved environmental impact: HDPE tubing is already known for its environmental benefits, including being recyclable and having a low carbon footprint. Recent advancements have further improved the environmental impact of HDPE tubing by reducing the amount of energy required to produce it and making it easier to recycle.
Overall, advancements in HDPE tubing technology have expanded its range of applications, improved its performance and durability, and made it an even more sustainable and environmentally-friendly choice for a wide range of industries and applications.
Chemical Resistance of HDPE Tubing
HDPE tubing has excellent chemical resistance, which is one of its key advantages. It is resistant to a wide range of chemicals, including acids, bases, salts, and alcohols. Here are some of the specific chemicals that HDPE tubing is resistant to:
- Acids: HDPE tubing is resistant to a wide range of acids, including sulfuric acid, hydrochloric acid, and nitric acid.
- Bases: HDPE tubing is also resistant to bases, such as sodium hydroxide and potassium hydroxide.
- Salts: HDPE tubing is resistant to a variety of salts, including sodium chloride, potassium chloride, and calcium chloride.
- Alcohols: HDPE tubing is resistant to a range of alcohols, including methanol, ethanol, and isopropanol.
- Hydrocarbons: HDPE tubing is resistant to many hydrocarbons, such as gasoline, diesel fuel, and lubricating oils.
In addition to these chemicals, HDPE tubing is also resistant to many other substances, including most solvents, detergents, and cleaning agents. This makes it a popular choice for use in a wide range of industrial and commercial applications, where it may come into contact with various chemicals and substances.
It is important to note, however, that HDPE tubing may not be resistant to all chemicals. It is always important to check the chemical compatibility of HDPE tubing with the specific chemicals it will be exposed to in order to ensure its performance and durability.
Joining HDPE Tubing
Joining HDPE tubing is a critical step in many applications where a continuous length of tubing is required. There are several methods for joining HDPE tubing, each with its own advantages and disadvantages. Here are some of the most common methods for joining HDPE tubing:
- Butt fusion: Butt fusion is a widely used method for joining HDPE tubing. This method involves heating the ends of the tubing to a molten state and then pressing them together until they fuse. This creates a strong and permanent joint that is leak-proof and resistant to chemicals and other environmental factors.
- Electrofusion: Electrofusion is another method for joining HDPE tubing, which involves using an electrofusion welding machine to heat and fuse the ends of the tubing. This method is particularly useful for joining tubing of different sizes and shapes.
- Compression fittings: Compression fittings are a simple and effective method for joining HDPE tubing. This involves inserting a compression fitting into the ends of the tubing and then tightening it to create a secure seal. Compression fittings are easy to install and do not require any special tools or equipment.
- Flanged joints: Flanged joints are commonly used in industrial applications where a high level of strength and reliability is required. This involves attaching flanges to the ends of the tubing and then bolting them together to create a secure joint.
- Mechanical couplings: Mechanical couplings are another method for joining HDPE tubing, which involves using a mechanical coupling to connect the ends of the tubing. This method is quick and easy to install and can be used to join tubing of different sizes.
Overall, the choice of joining method depends on the specific application and the requirements for strength, durability, and ease of installation. Each method has its own advantages and disadvantages, and it is important to choose the appropriate method to ensure the performance and reliability of the HDPE tubing.
Design Considerations for HDPE Tubing
When designing with HDPE tubing, there are several important considerations to keep in mind. Here are some of the key design considerations for HDPE tubing:
- Pressure rating: HDPE tubing is available in a range of pressure ratings, and it is important to choose the appropriate pressure rating for the application. This will depend on factors such as the fluid being transported, the temperature, and the flow rate.
- Temperature range: HDPE tubing has a maximum temperature range, beyond which it may begin to degrade or lose its structural integrity. It is important to choose a tubing material that can withstand the maximum temperature of the application.
- UV resistance: HDPE tubing is susceptible to damage from UV radiation, which can cause it to degrade over time. It is important to choose a tubing material that is UV resistant if the tubing will be exposed to sunlight or other sources of UV radiation.
- Chemical compatibility: HDPE tubing is resistant to a wide range of chemicals, but it may not be compatible with all chemicals. It is important to check the chemical compatibility of the tubing with the fluid being transported to ensure that it will not degrade or react with the fluid.
- Flexibility: HDPE tubing is flexible and can be easily bent and shaped to fit into tight spaces. However, excessive bending or twisting can cause the tubing to kink or collapse. It is important to design the tubing layout to minimize sharp bends and twists.
- Abrasion resistance: HDPE tubing is resistant to abrasion, but it may still be susceptible to damage from rough surfaces or sharp objects. It is important to choose a tubing material that has the appropriate level of abrasion resistance for the application.
- Installation method: The method of joining and installing the HDPE tubing can affect its performance and durability. It is important to choose the appropriate installation method based on factors such as the pressure rating, temperature range, and chemical compatibility.
Overall, designing with HDPE tubing requires careful consideration of the application requirements and the properties of the tubing material. By keeping these design considerations in mind, it is possible to create a reliable and durable tubing system that will perform well in a wide range of applications.
Applications of HDPE Tubing
HDPE tubing, or high-density polyethylene tubing, has a wide range of applications in various industries, thanks to its excellent combination of strength, flexibility, and chemical resistance. Here are some of the most common applications of HDPE tubing:
- Water and gas distribution systems: HDPE tubing is commonly used in water and gas distribution systems because of its high strength and durability. It is also resistant to corrosion, making it ideal for use in underground piping systems.
- Chemical processing: HDPE tubing's high resistance to chemicals, including acids, bases, and solvents, makes it an ideal choice for many chemical processing applications, such as those found in the pharmaceutical, food and beverage, and petrochemical industries.
- Geothermal systems: HDPE tubing is commonly used in geothermal systems because of its ability to withstand high temperatures and pressures. It is also highly resistant to chemicals and UV radiation, making it a durable option for underground piping systems.
- Agricultural irrigation systems: HDPE tubing is often used in agricultural irrigation systems because of its flexibility, which allows it to be easily bent and shaped to fit specific applications. It is also resistant to UV radiation and chemicals, making it a durable option for outdoor use.
- Mining and industrial applications: HDPE tubing is commonly used in mining and industrial applications because of its high strength and durability. It is also resistant to chemicals, making it an ideal choice for use in harsh environments.
- Medical and laboratory applications: HDPE tubing is commonly used in medical and laboratory applications, such as blood transfusion and fluid handling systems, because of its high chemical resistance and low toxicity.
Overall, the versatility and durability of HDPE tubing make it a popular choice for a wide range of industrial, commercial, and residential applications.
Conclusion
HDPE tubing is a versatile and widely used material in many industries, thanks to its excellent combination of properties such as high strength, chemical resistance, and flexibility. It is commonly used in applications such as water and gas distribution, irrigation, and industrial fluid handling.
Designing and working with HDPE tubing requires careful consideration of factors such as pressure rating, temperature range, chemical compatibility, flexibility, and installation method. By taking these factors into account, it is possible to create a reliable and efficient tubing system that meets the specific needs of the application.
Advancements in HDPE tubing technology continue to improve its properties and expand its applications, making it an increasingly popular choice for a wide range of industries. With proper design, installation, and maintenance, HDPE tubing can provide many years of reliable and efficient service.
read more :
Polyethylene Pipe (PE pipe)Polyethylene fittings
Polyethylene manhole
Technical Data