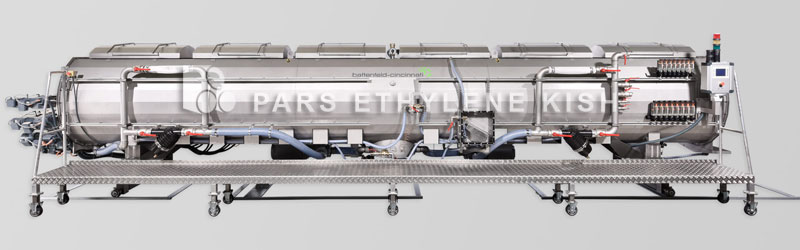
Vacuum Tank
Vacuum Tank of Polyethylene pipe Production Line
Vacuum tank is located after the Die Head and before the ultrasonic device and cooling tanks, and molten polyethylene material, after passing Die (Die Head), become pasty, and these pasty-shaped materials should pass through vacuum tank, and by this work, initial shape of the polyethylene pipe, is formed. At this stage, initial cooling is done, and polyethylene pipe will have a steady shape. This is a very important step, and pressure of the vacuum tank, water spray status and water temperature are very important, and polyethylene pipe in the vacuum tank, gets its final shape. In the vacuum tank, water spray is also performed, and cooling of the produced polyethylene pipe, starts from this stage (vacuum tank), and this cooling with water, only on the outer wall of the pipe is done, and for thick and large size pipes, this cooling system (water spray on the outer wall) is not enough, and it may have a negative impact on the inner wall. Some extruders have an Air Cooling system, that in this system, air cools inside of the pipe, and hot and warm air of inside pipe in production, removed by sucker fans. All Extruders of Pars Ethylene Kish have Air Cooling Technology.
Vacuum tank must be made of stainless steel or steel, and can be painted after production. Based on capacity of the extruder in the production line of polyethylene pipes and need for subsequent cooling, capacity, volume and size of the vacuum tanks are designed and installed.
Vacuum tanks, vacuum reservoir or vacuum tubes are all other names of the vacuum tank.
Suction Machine
Gravimetric
Extruder
Monitoring of polyethylene pipe production line
Polyethylene pipe mold
Vacuum Tank
Ultrasonic
Cooling Tank
Haul off of Polyethylene pipe
Polyethylene pipe marker
Saw
Tilling Table
PIPE Winder
Equipment for production line of polyethylene pipes and connections
Production line of single wall polyethylene pipes
Double wall polyethylene Corrugated Pipe production line
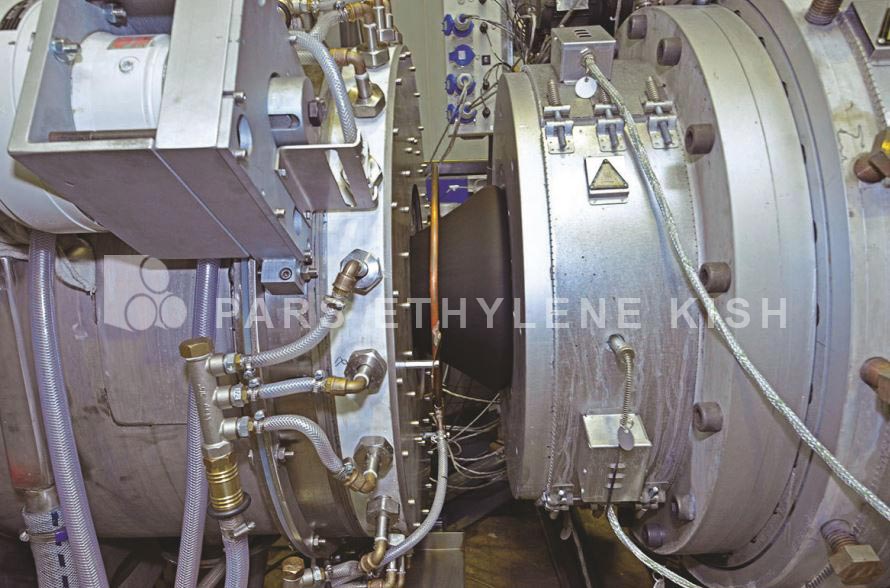

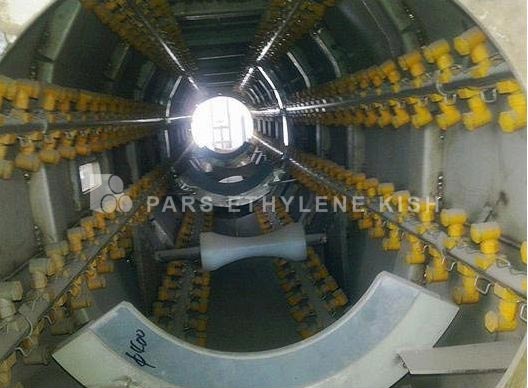



