polyethylene in the packaging industry
-
Introduction
-
Definition of Polyethylene
-
Brief History of Polyethylene in the Packaging Industry
-
Importance of Polyethylene in the Packaging Industry
-
-
Types of Polyethylene Used in the Packaging Industry
-
Low Density Polyethylene (LDPE)
-
High Density Polyethylene (HDPE)
-
Linear Low Density Polyethylene (LLDPE)
-
Medium Density Polyethylene (MDPE)
-
-
Properties of Polyethylene
-
Physical Properties
-
Mechanical Properties
-
Thermal Properties
-
Chemical Properties
-
-
Manufacturing Process of Polyethylene
-
Polymerization
-
Extrusion
-
Blown Film Process
-
Cast Film Process
-
Injection Molding
-
Thermoforming
-
Applications of Polyethylene in the Packaging Industry
-
Flexible Packaging
-
Rigid Packaging
-
Bags and Sacks
-
Wraps and Films
-
Bottles and Containers
-
Advantages and Disadvantages of Polyethylene in the Packaging Industry
-
Future of Polyethylene in the Packaging Industry
-
Innovations in Polyethylene Manufacturing
-
Trends in Polyethylene Applications
-
Environmental Concerns and Sustainability of Polyethylene
-
Conclusion
-
Summary of Key Findings
-
Recommendations for Future Research
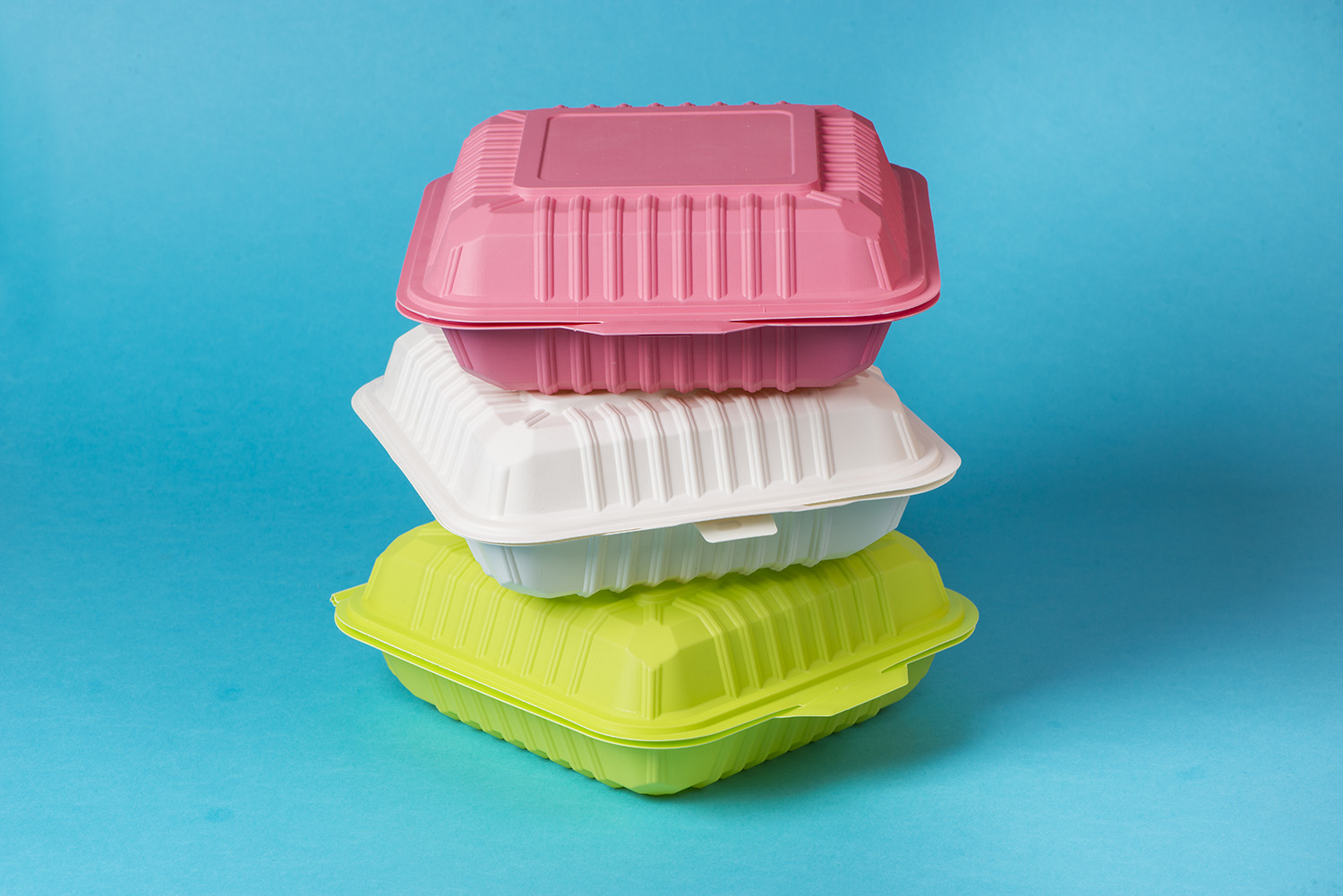
Introduction:
Polyethylene is one of the most widely used thermoplastics in the world, and its applications in the packaging industry are vast. Polyethylene's unique combination of properties, such as flexibility, durability, chemical resistance, and low cost, make it an ideal material for a wide range of packaging applications, from flexible packaging films to rigid plastic containers.
Over the years, the packaging industry has continued to evolve, with new and innovative packaging materials being developed to meet the changing needs of consumers and manufacturers. Despite the emergence of other materials like biodegradable plastics, polyethylene remains a key player in the packaging industry due to its affordability, ease of processing, and versatility.
This study aims to explore the different types of polyethylene used in the packaging industry, their properties, manufacturing processes, applications, advantages, and disadvantages. Furthermore, the study will highlight the future of polyethylene in the packaging industry, including emerging trends and innovations, as well as environmental concerns and sustainability challenges. By doing so, this study will provide a comprehensive overview of the role of polyethylene in the packaging industry, and offer insights into the opportunities and challenges that lie ahead.
Certainly, here's an overview of the different types of polyethylene used in the packaging industry:
Types of Polyethylene Used in the Packaging Industry:
Polyethylene can be broadly classified into four different types based on its density and branching structure, which determines its properties and processing characteristics. The four types are:
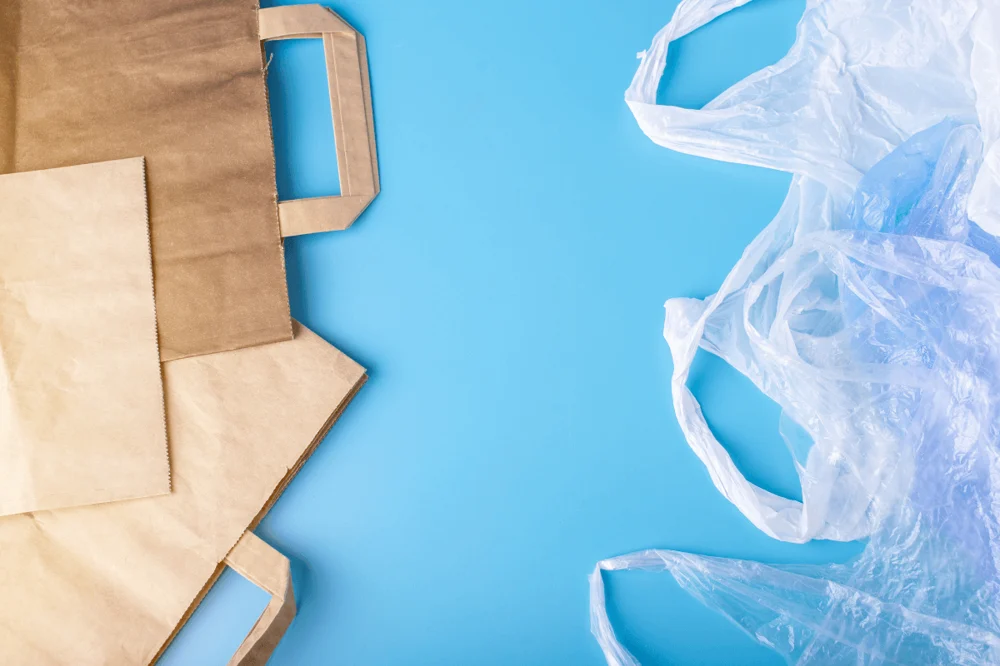
1. Low Density Polyethylene (LDPE):
LDPE is the most common type of polyethylene used in the packaging industry due to its excellent flexibility, toughness, and transparency. LDPE is commonly used to produce flexible packaging films, bags, and liners, as well as squeeze bottles and other containers. It is also highly resistant to chemicals, making it suitable for applications that require contact with acidic or alkaline substances.
2. High Density Polyethylene (HDPE):
HDPE is a more rigid and durable form of polyethylene, with a higher density and greater strength than LDPE. HDPE is commonly used in the production of rigid packaging containers, such as milk jugs, shampoo bottles, and detergent bottles. It is also used to make pipes, fittings, and other construction materials.
3. Linear Low Density Polyethylene (LLDPE):
LLDPE is a more recently developed form of polyethylene that combines the best properties of both LDPE and HDPE. It is more flexible than HDPE, yet stronger and more durable than LDPE, making it suitable for a wide range of applications in the packaging industry, including stretch films, heavy-duty bags, and liners.
4. Medium Density Polyethylene (MDPE):
MDPE is a medium-density form of polyethylene that is used primarily in the production of gas pipes and fittings, as well as irrigation tubing. Its properties fall somewhere between those of LDPE and HDPE, making it suitable for a range of applications that require moderate strength and flexibility.
Overall, the choice of polyethylene type depends on the specific requirements of the packaging application, such as the desired strength, flexibility, transparency, and chemical resistance.
Certainly, here's an overview of the properties of polyethylene:
Properties of Polyethylene:
Polyethylene possesses a unique combination of physical, mechanical, thermal, and chemical properties that make it an ideal material for a wide range of packaging applications. Some of the key properties of polyethylene include:
1. Physical Properties:
Polyethylene is a thermoplastic polymer that is lightweight, flexible, and transparent. It is also highly resistant to moisture and water vapor, which makes it ideal for packaging applications that require a barrier against these elements.
2. Mechanical Properties:
Polyethylene has good tensile strength, which allows it to resist tearing and puncturing. It is also highly flexible, which makes it suitable for applications that require a high degree of elasticity, such as stretch films.
3. Thermal Properties:
Polyethylene has a relatively low melting point, which makes it easy to process using various methods such as extrusion, injection molding, and blow molding. It is also highly resistant to heat and cold, which makes it suitable for applications that require exposure to extreme temperatures.
4. Chemical Properties:
Polyethylene is highly resistant to most chemicals, including acids, bases, and organic solvents. It is also highly resistant to UV radiation, which makes it ideal for outdoor applications that require exposure to sunlight.
Overall, the properties of polyethylene can vary depending on the type and grade of polyethylene used, as well as the specific application requirements. However, polyethylene's unique combination of properties makes it one of the most versatile and widely used packaging materials in the world.
Certainly, here's an overview of the manufacturing process of polyethylene:
Manufacturing Process of Polyethylene:
Polyethylene is typically manufactured using a process called polymerization, which involves the chemical reaction of ethylene gas to form long chains of polyethylene molecules. The two main methods of polyethylene production are:
1. High-pressure polymerization:
In this method, ethylene gas is compressed and heated to high pressures and temperatures in the presence of a catalyst, typically a combination of oxygen and a transition metal, such as titanium or chromium. The high pressure causes the gas molecules to bond together to form long chains of polyethylene. This process is used to produce LDPE.
2. Low-pressure polymerization:
In this method, ethylene gas is reacted with a catalyst, such as Ziegler-Natta or metallocene, at lower pressures and temperatures. The catalyst helps to control the polymerization reaction and produce a more uniform product. This process is used to produce HDPE, LLDPE, and MDPE.
After the polymerization process, the polyethylene is typically extruded into various forms, such as films, sheets, or pellets. The polyethylene can also be further processed using techniques such as injection molding or blow molding to produce various shapes and sizes of plastic products.
Overall, the manufacturing process of polyethylene is highly dependent on the type and grade of polyethylene being produced, as well as the specific manufacturing equipment and processes used.
Certainly, here's an overview of the applications of polyethylene in the packaging industry:
Applications of Polyethylene in the Packaging Industry:
Polyethylene is one of the most widely used packaging materials in the world, owing to its versatility, affordability, and wide range of properties. Some of the key applications of polyethylene in the packaging industry include:
1. Flexible Packaging:
Polyethylene is commonly used to produce flexible packaging films, bags, and liners for a wide range of products, including food, beverages, pharmaceuticals, and consumer goods. LDPE and LLDPE are particularly well-suited for flexible packaging applications, owing to their excellent flexibility and low density.
2. Rigid Packaging:
Polyethylene is also used to produce a range of rigid packaging containers, such as bottles, jars, and tubs. HDPE is commonly used for these applications due to its high strength and durability.
3. Agricultural Packaging:
Polyethylene is used extensively in the agricultural industry for packaging and protecting crops, such as fruits and vegetables. LDPE is often used to produce agricultural films, such as mulch films, greenhouse films, and silage bags.
4. Industrial Packaging:
Polyethylene is used in a wide range of industrial packaging applications, such as shrink films, stretch films, and pallet wrap. LLDPE is often used for these applications due to its high strength and flexibility.
5. Medical Packaging:
Polyethylene is used extensively in the medical industry for packaging and protecting medical devices and products. LDPE and LLDPE are often used for these applications due to their excellent chemical resistance and low toxicity.
Overall, the applications of polyethylene in the packaging industry are vast and varied, owing to its unique combination of properties and versatility. Polyethylene is expected to continue to be a key material in the packaging industry for many years to come.
Certainly, here's an overview of the advantages and disadvantages of using polyethylene in the packaging industry:
Advantages and Disadvantages of Polyethylene in the Packaging Industry:
Advantages:
1. Versatility: Polyethylene is a highly versatile material that can be used for a wide range of packaging applications.
2. Cost-effective: Polyethylene is one of the most affordable packaging materials on the market, making it an attractive option for businesses looking to reduce costs.
3. Light-weight: Polyethylene is lightweight, which makes it easy to transport and reduces shipping costs.
4. Chemical resistance: Polyethylene is highly resistant to most chemicals, making it suitable for a wide range of packaging applications.
5. Recyclable: Polyethylene can be easily recycled, making it an environmentally friendly option for businesses.
Disadvantages:
1. Environmental impact: Polyethylene is not biodegradable and can take hundreds of years to decompose, leading to environmental concerns.
2. Limited heat resistance: Polyethylene has a relatively low melting point and may not be suitable for high-temperature applications.
3. Low stiffness: Polyethylene may not be suitable for packaging applications that require a high degree of stiffness or rigidity.
4. Limited UV resistance: Polyethylene may degrade when exposed to sunlight, which can limit its use in outdoor applications.
Overall, polyethylene offers a wide range of advantages as a packaging material, including its versatility, cost-effectiveness, and chemical resistance. However, it also has some notable disadvantages, such as its limited heat resistance and environmental impact, which businesses should consider when evaluating its use.
Certainly, here's an overview of the future of polyethylene in the packaging industry:
Future of Polyethylene in the Packaging Industry:
Polyethylene is expected to continue to be a key material in the packaging industry for the foreseeable future, owing to its unique combination of properties and versatility. Some of the key trends that are expected to shape the future of polyethylene in the packaging industry include:
1. Sustainable Packaging:
The demand for sustainable packaging solutions is expected to continue to grow, as consumers become increasingly aware of the environmental impact of packaging. Polyethylene is already a relatively sustainable packaging material, due to its recyclability, but there is a growing need for more eco-friendly alternatives, such as biodegradable or compostable plastics.
2. Advanced Processing Technologies:
Advances in processing technologies are expected to continue to improve the performance and properties of polyethylene, making it an even more attractive packaging material. For example, new catalysts and polymerization processes are being developed that can produce polyethylene with enhanced properties, such as improved strength, stiffness, and heat resistance.
3. Use of Nanotechnology:
Nanotechnology is expected to play an increasingly important role in the development of polyethylene-based packaging materials, as it allows for the creation of materials with unique properties and functionality. For example, the use of nanoparticles can enhance the strength, barrier properties, and UV resistance of polyethylene films.
4. Digital Printing:
Digital printing is expected to revolutionize the packaging industry, allowing for more efficient and flexible production of packaging materials. Polyethylene is a popular material for digital printing due to its ability to accept ink and its excellent printability.
Overall, the future of polyethylene in the packaging industry is bright, with continued demand for this versatile and cost-effective material. However, businesses will need to stay abreast of the latest developments in processing technologies, nanotechnology, and sustainable packaging solutions to remain competitive in this rapidly evolving industry.
In conclusion, polyethylene is a highly versatile and widely used material in the packaging industry. It offers a unique combination of properties, including chemical resistance, light weight, and cost-effectiveness, that make it an attractive option for businesses of all sizes. However, there are also some notable disadvantages to using polyethylene, such as its limited heat resistance and environmental impact.
Despite these limitations, polyethylene is expected to remain a key material in the packaging industry for the foreseeable future, thanks to ongoing advances in processing technologies, nanotechnology, and sustainable packaging solutions. As businesses seek to reduce costs, improve performance, and meet the growing demand for sustainable packaging, polyethylene is likely to play an even more important role in the years to come.
Overall, businesses that are looking to use polyethylene in their packaging applications should carefully consider its properties and limitations, and seek out the latest developments in processing technologies and sustainable packaging solutions to stay ahead of the curve.