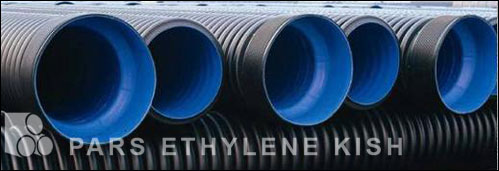
Functional Principles of Corrugator Technology
Machinery of PE Double wall pipes
► Functional principle of die heads in corrugated pipe production with one extruder
This method of production for double wall pipes, whose inner and outer layers are
being extruded from the same material supplied from one extruder, is an especially economical design. The below die head has material flow divided by the spider into material for inner and outer layer.
This die head was especially manufactured for pipes made of polyolefin such as PE and PP. The extruded material is split up here in the material distributor box and is controlled via bolts.
Therefore an individual adjustment of the material supply for the inner and outer wall of the pipe is enabled.
► Functional principle of die heads in the production with two extruder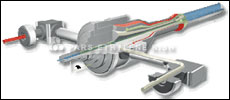
One extruder for the pipe external wall, one extruder for the pipe internal wall. Thereby, you have the possibility to use different materials for each pipe layer, to use different colors and to produce flexible pipes.
Immediately after the forming process of the profiles outer layer, the smooth inner layer of the pipe is extruded. Thereby, the high static loading capacity is achieved by means of the homogeneous welding.
Disc die head for pipes with an outer diameter of up to 2000 mm. This construction unites the following advantages due to the relatively short die
head:
• lower weight of the die head
• shorter flow channels
• lower energy consumption
• simple control of the material temperature
• higher output
• easier handling
This technology of die head can also be utilized together with a material distributor box using one extruder.
► Functional principle of die heads in the production of triple wall pipes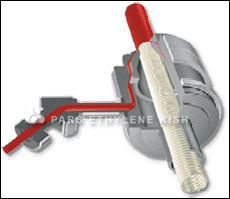
An additional smooth outer layer is put on the corrugated pipe using a cross die head. Often this will then be run through a traditional vacuum sizing tank with a puller and cutoff downstream from the tank. In applications not requiring a smooth outer wall the pipe can be run without a sizing tank.
The use of a cross head die is not limited to making triple wall pipes, but could also be used in the production of technical parts with varying insert sections.
► Corrugator with a closed mold block channel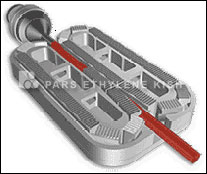
Corrugators with a pipe diameter of up to 65 mm are built in closed construction, this allows for very high production speed at a high smoothness of running and continuous lubrication.
They are typically water cooled using a water jacketing method to enclose the mold blocks. This style of corrugator has been a work horse in the automotive wiring harness industry.
► Corrugator with an open mold block channel
Due to the open horizontal construction, the mold blocks
are installed on a chain of mold block carriers.They do not run in closed channels but on a horizontal plate, equipped with guiding rails. The guiding rails combined with a synchronized upper and lower mold block drive, guarantee an exact positioning of the mold blocks in the middle channel and thereby assuring a high pipe quality Due to the open construction and to the mold block design, the mold block change-over has become much easier and faster as only one screw has to be loosened.
► Shuttle corrugator principal
In the UNICOR shuttle system, the mold blocks in the retu
rn channel are not sent back to the middle channel in a closed chain at the same speed. They are sent back individually with increased return speed. This reduces the number of required mold blocks and thus the cost of investment.
The reversing of the mold blocks at the inlet and outlet of the middle channel does not take place in guiding curves. The mold blocks are carried to the inlet and the outlet of the middle channel in a right angle, hereby the width of the machine is reduced. The entire movement of the mold blocks is carried out by servo-motors and is SPS-controlled. This guarantees the highest smoothness of running and an excellent product quality.
► Mold Blocks for pipe corrugator machines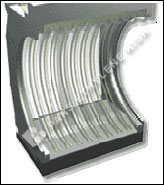
Vacuum mold blocks are recommended for a majority of the products:
• uniform distribution of the wall thickness
• unlimited possibilities of the pipe profile or part geometry
• better production tolerances
• excellent finished part surface
• increases the production speeds with better plastic to mold contact
• allows higher use of recycled materials in polymer.
► Mold Block styles for pipe corrugators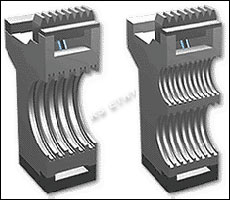
On the inside, the mold blocks show the negative of the profile of the produced pipe as per the profile drawing and upon request with engravings for marking. For making certain diameters, we are also able to put more profiles in one mold block. Thus you save change-over time as well as the costs of additional mold block sets.
► The cooling system of closed channel pipe corrugators
The walls of the middle channel and of the return line of the mold blocks are uniformly drizzled with cooling water dealing with the spray cooling.
The more efficient the cooling of the mold blocks is, the higher is the production speed and/or the shorter the mold block chains can be.
► Mold block cooling for the corrugator range of 500 mm to 2000 mm outer diameter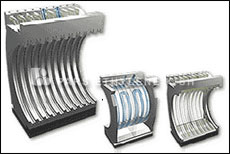